覚えておきたい製剤技術の基礎知識! 第1章:製剤とは? FREUND Academy 2022.10.06
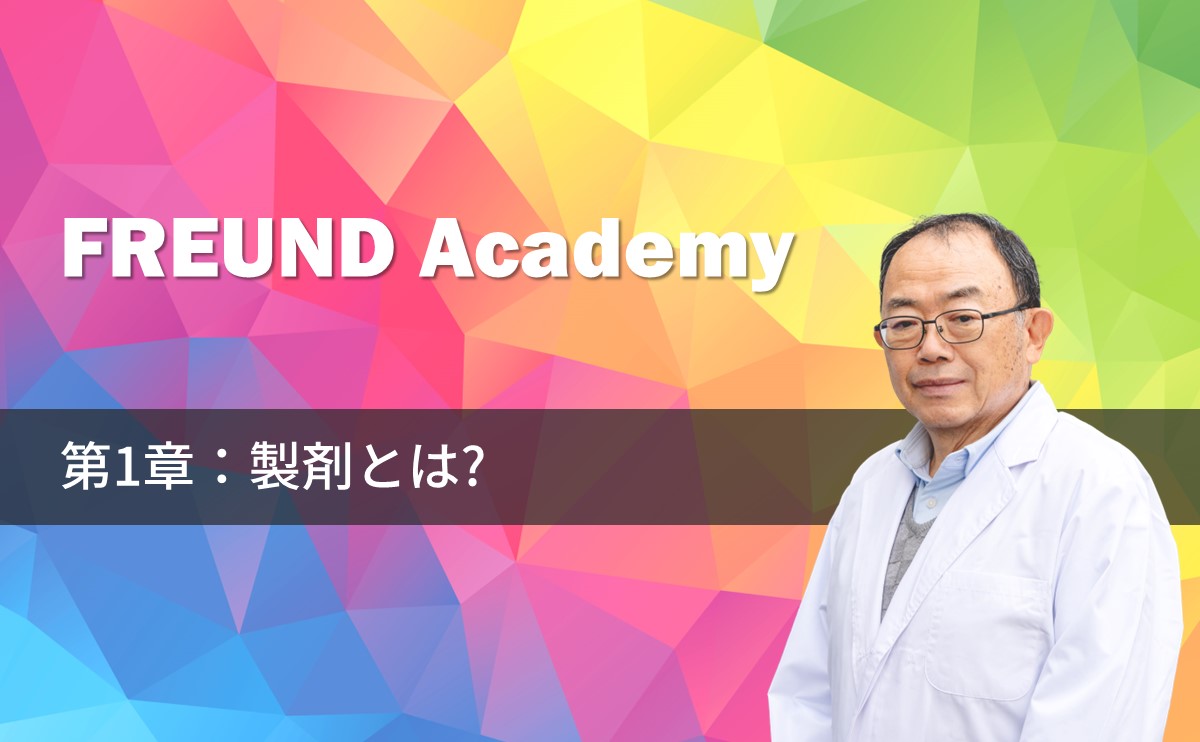
FREUND KNOWLEDGE OCEANをご覧頂き誠にありがとうございます。
FREUND Academy Instructorの武井でございます。
製剤業務に従事される新任研究者・技術者の皆さま、ならびにその上司の皆さま
お客様から寄せられる「改めて製剤についての基礎的な知識を学びたい」「OJTでの技術習得と並行して知識を学んで欲しい」というご要望にお応えし、製剤に関するベーシックな知識を学んでいただけるコンテンツ "FREUND Academy" をスタートいたします。
製剤装置と添加剤の双方を開発・製造・販売している当社だからこそ培うことのできた知識を、全10章に分けてお送りいたします。
もちろん、新任研究者・技術者の方だけではなく、その先輩・上司の皆さまも復習としてお役立て頂ければ幸いです。
どうぞ最後までお付き合いください。
1.1 製剤の定義
製剤とは、医薬品を服用に適した形状に加工する工程そのものを示す用語であるとともに、得られた製品を示す用語でもあります。FREUND Academyでは、経口固形製剤(口から投与される錠剤やカプセル剤、顆粒剤などの固体医薬品)について説明します。参考のため、化学合成される経口固形製剤の原薬と製剤の関係を 図1 に示します。薬の主成分そのものは「原薬」と呼ばれますが、製剤工程では「主薬」と呼ばれることもあります。
製剤工程では、主薬を服用しやすくする工夫(苦味のマスキングや口腔内崩壊錠など)がなされます。また、主薬をより有効に作用させる工夫(徐放化、腸溶化など)も行われます。
1.2 剤形
2021年6月に告示された第18改正日本薬局方の製剤総則(3)製剤各条では、剤形は投与経路別に11種類に分類され、剤形の定義、製法、試験法、容器、包装及び貯法が示されています。製剤各条に記載されている剤形の分類を 図2 に示します。多くの剤形が記載されていますが、錠剤、顆粒剤、散剤、カプセル剤、注射剤、軟膏剤などが汎用されています。また、たとえば1.経口投与する製剤の錠剤の項目には、一般的な錠剤のほか、①口腔内崩壊錠、②チュアブル錠、③発泡錠、④分散錠、⑤溶解錠が含まれると記載され、図2の剤形がさらに小分類されています。
1.3 製剤ができるまでの流れ
製剤開発の流れを 図3 に示します。製剤には安全で服用しやすいことが望まれますが、そのために、まず剤形を決定する必要があり、剤形決定には投与経路の選択が不可欠です。
そして、投与経路の選択には原薬の物性が大きく関与します。たとえば、胃酸により分解する原薬には、腸溶性の製剤化が望まれます。したがって、製剤開発は原薬物性の調査から始まります。
消化管内における原薬の溶解度や吸収特性により、投与経路や剤形を選定します。
剤形が決まったら、つぎに処方を決定します。処方決定には添加剤の選定が重要になり、薬効を有効に発現させるための製剤工夫(溶解度の改善、放出制御など)や服用しやすくするための製剤工夫(苦味マスキングや口腔内崩壊錠など)が考慮されます。
剤形、処方の次は製造法の検討です。錠剤やカプセル剤など経口固形製剤では、通常、混合-造粒-乾燥などの工程が考えられます。製剤化工程は複数の単位操作で構成され、単位操作ごとに専用の製造機械があり、それぞれ製造条件の確立が必要になります。製剤開発の初期は少量の原料を用いて、小型機械で製造条件が検討されます。
小型機械で製造方法が確立され、臨床試験用の製剤製造が行われると、いよいよ工業化の検討が開始されます。工業化検討では、それまでの小型機械を用いた製造方法をスケールアップして、小型機械で得られた製剤と同じ品質の製剤を製造することを目指します。
望ましい製剤品質を獲得するために、品質検査に裏付けられた製造条件の確立が求められます。
2.1 製剤工程
製剤工程は 図4 に示すよう主に3つに分類されます。1つは原薬を造粒、打錠することで経口固形製剤を作る工程です。2つ目は、原薬を溶解、ろ過することにより注射剤などの液剤にする工程です。3つ目は、原薬を軟膏基剤などと混合、展延して貼付剤やパップ剤などの外用剤を得る工程です。
経口固形製剤工程の概略を 図5 に示します。
(1)混合工程
計量された主薬と添加剤を均一に混ぜ合わせるのが混合工程です。粉粒体を混合するために、容器や撹拌羽根の回転が用いられることから、混合装置は容器回転式と機械撹拌式に大別されます。
混合工程を終了すると、多くの場合、次の造粒工程に進みますが、混合工程だけでも製品として散剤(粉末状の製剤)が得られます。
(2)造粒工程
混合された主薬と添加剤に、バインダー(結合剤)を用いて粒を造るのが造粒工程です。
造粒後に必要があれば整粒して粒度を調整します。
造粒装置は、湿式法と乾式法とに大別され、湿式造粒装置には、流動層造粒装置、撹拌造粒装置、遠心転動造粒装置、押出造粒装置、噴霧乾燥造粒装置などがあります。
図6 流動層造粒装置とは、粉体原料を円筒容器内で気流により浮遊懸濁させ、そこにバインダーを噴霧して粉体どうしを付着凝集させる造粒装置で、通常、バッチプロセスにより乾燥まで行われます。標準的仕様のほか、内部に円板や撹拌羽根を設置した装置や微粒子コーティング用の側方噴霧技術など多機能化されています。
図7 撹拌造粒装置とは、粉体原料を円筒やシェル型の容器内で、高速回転する撹拌羽根により混合撹拌しながら、バインダー液を加え、粉体どうしを付着凝集させる造粒装置です。乾燥は別装置(流動層乾燥装置、棚式乾燥装置など)で行います。
図8 遠心転動造粒装置では、装置に投入された核粒子は、回転円板から受ける遠心力と旋回力により、回転円板上で円弧を描きながら自転-公転運動(スパイラル運動)をします。遠心転動している核粒子にバインダーをスプレーしながら粉末を散布すると、核粒子表面に粉末が付着し、球形顆粒が得られます。粉末をバインダー中に懸濁させてスプレーする方法もでき、粒子コーティングにも適しています。
押出造粒装置は、あらかじめ湿潤させた原料をスクリーンから押し出して造粒します。押出機構にはスクリュー型やバスケット型があります。乾燥は別装置(流動層乾燥装置、棚式乾燥装置など)で行います。連続生産が注目されたことにより、装置メーカー各社がスクリュー型連続造粒装置の開発に注力しました。
噴霧乾燥造粒装置(スプレードライヤー)は、液状の原料を高温気流中で微粒化し、瞬時に乾燥を行い、粉粒体製品を得る造粒装置です。液体を微粒化する方法として、ロータリーディスク法とスプレーノズル法があります。
(3)打錠工程
造粒された半製品に滑沢剤を添加して製錠するのが打錠工程です。一般に使用されるロータリー(回転)式打錠機では、打錠工程は「充填工程」、「圧縮工程」、「排出工程」に細分されます。「充填工程」で顆粒を臼に供給し、「圧縮工程」で顆粒を臼の内部で圧縮成形し、「排出工程」で圧縮成形された錠剤を取り出します。これら3工程は臼杵が1回転する間に行われます。
高速で硬度の大きい錠剤を得るためには、流動性が良く、空隙率の大きな柔らかい(圧縮しやすい)顆粒が望ましいとされています。打錠された製剤は素錠と呼ばれ、そのまま製品化されるか、次のコーティング工程に進みます。
(4)コーティング工程
図11 コーティング工程は、錠剤表面に膜状あるいは層状に被覆物質を形成させる工程です。錠剤コーティングは、高分子皮膜を形成するフィルムコーティングと糖衣層を形成する糖衣コーティングに大別されます。
給気口から導入された空気は、パンチング板で形成されたパン円周部の斜め上部からコーティングパン内に流入します。装置内部にはスプレーノズルが設置され、転動する錠剤層に向けてコーティング液を噴霧します。錠剤層を通過した空気はコーティングパンの斜め下部に位置するパンチングから排気チャンバーを介して系外に排気されます。
(5)充填工程
充填工程とは散剤や顆粒剤を計量してハードカプセルに充填する工程です。コーティング錠と同様に、カプセル剤でも耐候性やマスキング効果を得ることができます。計量方式には重量式と容量式が採用されています。
(6)包装工程
上記の各工程により得られた製剤は、包装工程を経て初めて医薬品と呼ぶことができます。包装により耐候性が付与され、内容物の保護が可能になります。
2.2 製剤工夫
製剤工程では、医薬品の有効性改善、服用性改善、溶解性改善などの製剤的工夫が施されます。ここでは、製剤的工夫の一例として、(1)放出制御製剤と(2)口腔内崩壊錠について紹介します。
(1)放出制御製剤
素早く薬効を発現するためには、製剤の速溶化を行います。速溶性を付加するには、原薬の微粒化や結晶の非晶質化、固体分散体などの手法が使われます。固体分散体あるいは固溶体とは、化学物質(たとえば水溶性高分子)中に薬物を微粒子の状態で分散させたもの、あるいは溶解させたもので、薬物の溶解度が改善します。
長時間にわたり薬効を持続させる手法として、薬物の徐放化が採用されます。徐放性製剤では投与回数が減るので、患者の服薬アドヒアランス が向上し、副作用の低減が期待できます。薬物を含有した球形粒子それぞれに徐放性を施し、カプセルに充填したマルチプルユニット製剤の例を 図12 に示します。
(2)口腔内崩壊錠
嚥下する力が低下した患者向けに、口腔内で速やかに崩壊する錠剤があります。口腔内で唾液あるいは少量の水で崩壊するので、嚥下しやすいことが特徴です。薬物の苦味が強烈な場合、口腔内で薬物が溶解しないように、薬物微粒子にマスキングコートをしてから打錠成形します。コーティング微粒子を含有した口腔内崩壊錠の例を 図12 に示します。
↓↓↓ 更に詳しく学びたい方へ資料をご準備しております。下記よりダウンロード可能です ↓↓↓
3.1 品質設計
(1)品質の設計
固形製剤を設計する手順は、まず、原薬の物性や添加剤との相性を検討することから始まります。その次に、剤形を選択した上で、処方と製造プロセスを決定します。この場合、主成分の安定性や均一性が重要になります。また、バイオアベイラビリティ(Bioavailability)も考慮する必要があります。バイオアベイラビリティとは生物学的利用能と訳され、投与された薬物のうちに薬効が発現された割合を示します。
これら安定性、均一性、バイオアベイラビリティは、すなわち、投与された薬物がどのくらい薬効を発現するのかに影響します。
(2)設計変更とSUPAC
新薬の開発段階では、必ずしも処方が確立されていないことや、製造スケールが小規模な場合が考えられます。そのため、新薬の承認後、申請者が次のような変更を考える場合が想定されます。
①成分及び組成の変更、②製造場所の変更、③製造のスケールアップ/スケールダウン、④製造法(工程および装置)の変更。
FDA(米国食品医薬品局)により、こうした変更について規定が設けられています。このガイダンスはSUPAC(Scale-Up and Post-Approval Changes)と呼ばれ、経口固形製剤に適用されるガイダンスには、SUPAC -IR(Immediate Release)とSUPAC -MR(Modified Release)があります。
3.2 GMPとバリデーション
(1)GMP
医薬品の製造はGMP(Good Manufacturing Practice、医薬品の製造管理及び品質管理に関する基準)に準拠して行うことが法制されています。①人による間違いを最小限にする、②医薬品の汚染、品質低下を防ぐ、③高い品質を保つ仕組みをつくる、これらがGMPの三原則と言われています。
(2)バリデーション
GMPの基準を科学的に検証する方法がバリデーションです。バリデーションには、①適格性評価、②プロセスバリデーション(予測的バリデーション、コンカレントバリデーション)、③洗浄バリデーション、④再バリデーション、⑤変更時のバリデーションがあります。
①適格性評価
設備、機器のバリデーションで、DQ(Design Qualification):設計時適格性評価、IQ(Installation Qualification):設備据付時適格性評価、OQ(Operational Qualification):運転時適格性評価、PQ(Performance Qualification):性能適格性評価があります。
②プロセスバリデーション
商業生産の各条件の妥当性を実生産規模で検証するバリデーションです。
予測的バリデーション:製品の通常生産前に行われるバリデーションです。
コンカレントバリデーション:製品の通常生産に合わせて行うバリデーションです。
③洗浄バリデーション
交差汚染や異物混入を防止するため、洗浄方法の妥当性を検証するバリデーションです。
④再バリデーション
製品品質が恒常的に適合していることを検証するバリデーションです。
⑤変更時のバリデーション
原材料、製造工程、製造設備などを変更する場合に行うバリデーションです。
3.3 国際調和(ICHとPIC/S)
(1)ICHとは?
日本・米国・ヨーロッパでは、医薬品の承認に際し、それぞれの審査基準が異なるため、新規医薬品を迅速にグローバル展開する上での障害になっていました。安全で有効な新医薬品をより早く提供するため、各地域の医薬品承認審査の基準を標準化することが必要となり、1990年4月、日本・米国・ヨーロッパの各医薬品規制当局と業界団体によりICHが発足しました。
ICHとは、International Council for Harmonisation of Technical Requirements for Pharmaceuticals for Human Use(医薬品規制調和国際会議)の略称です。これまでに多くのガイドラインが作成され、規制の国際調和が進んでいます。
(2)PIC/Sとは?
規制の国際調和と同様に、GMPについても国際調和が検討されました。
PIC/Sは、Pharmaceutical Inspection Convention and Pharmaceutical Inspection Co-operation Scheme(医薬品査察協定および医薬品査察共同スキーム)の略称です。PIC/Sでは、医薬品分野における国際的に調和されたGMP基準および査察業務における品質システムの開発・実施・保守を目的としています。
参考文献
・製剤機械技術学会:製剤機械技術ハンドブック
・永井恒司ほか:CMCの実際、じほう(2003)
第1章:製剤とは?を最後までお読み頂きありがとうございました。
第2章は「造粒と乾燥」をお届けする予定です。
このコンテンツが製薬業界の更なる進歩発展の一助となれますよう、心を込めて執筆いたします。
次回もお付き合いくださいますよう、よろしくお願い申し上げます。
↓↓↓ 更に詳しく学びたい方へ資料をご準備しております。下記よりダウンロード可能です ↓↓↓ ※上記、記事中の物と同一のダウンロード資料です。
キーワード: