覚えておきたい製剤技術の基礎知識! 第2章:造粒と乾燥 FREUND Academy 2022.12.12
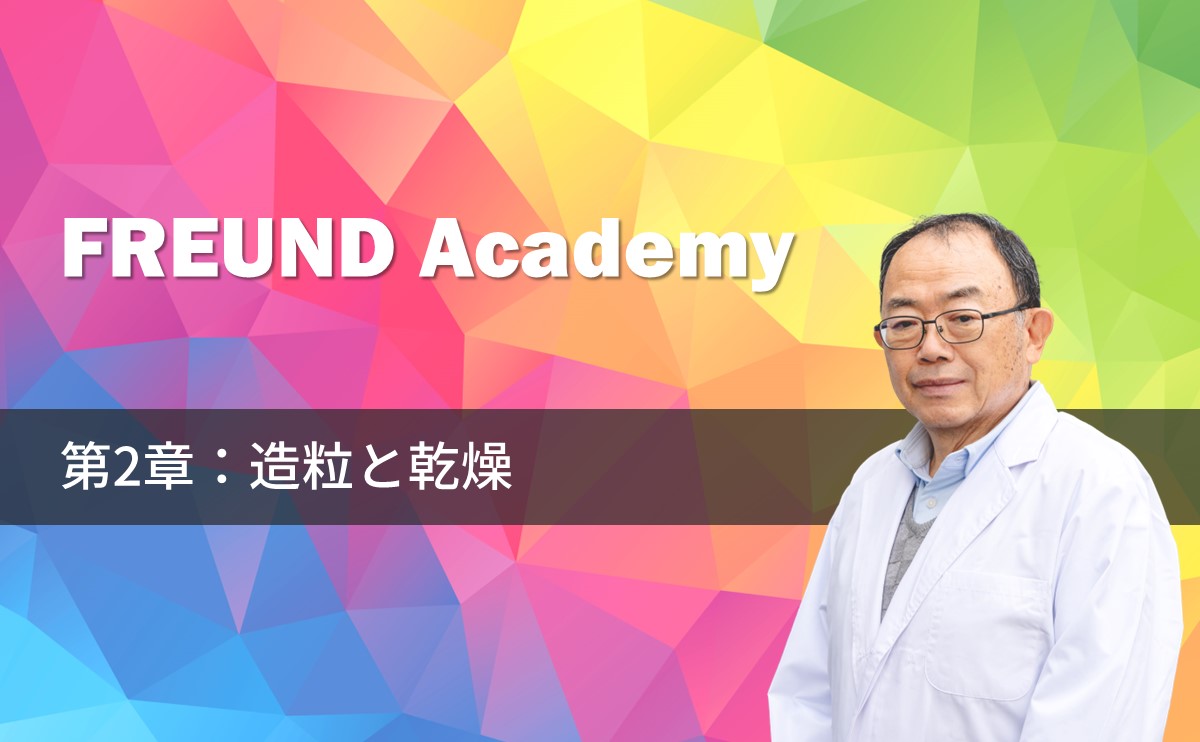
FREUND KNOWLEDGE OCEANをご覧頂き誠にありがとうございます。
FREUND Academy Instructorの武井でございます。
このFREUND Academyでは、製剤に関するベーシックな知識を全10章に分けてお送りいたします。
第2章のテーマは造粒と乾燥。
皆さまにお役立て頂けるホワイトペーパーもございますので、今回も最後までお付き合いください。
未読の方は、第1章:製剤とは? も是非ご覧ください。
-
1.造粒コーティング技術とは
1.1 造粒技術の定義
1.2 造粒コーティングの目的
1.3 造粒メカニズムの分類
2.製薬業界における造粒
2.1 造粒の目的
2.2 製造方法の選択
3.凝集造粒と乾燥の基礎理論
3.1 固-液系充填構造
3.2 凝集造粒のメカニズム
3.3 乾燥プロセス
1.1 造粒技術の定義
造粒とは、文字通り粒をつくる操作のことを言います。
コナ(粉)、ツブ(粒)およびカタマリ(塊)などの用語は、業界によって定義に多少の差はありますが、粒径が100μm以下をコナ(粉)、数mm以上をカタマリ(塊)、両者の中間をツブ(粒)と呼ぶのが一般的です(図1)。
したがって、『造粒』とは100μm以上数mm以下の固体を造る操作であり、粒径増大法(Size enlargement)と粒径細分法(Size reduction)の2つに分類されます。
また、粉を大きくして粒を造る技術と、塊を小さくして粒を造る技術を総称して、造粒技術と呼び、粒子表面に適当な物質を被覆するコーティング技術やカプセル化技術も造粒技術に包含されます。
1.2 造粒コーティングの目的
(1)造粒の目的
造粒の目的は、主に次の6つです。
①流動性の向上
粒は、粉や塊よりも流動性が良いので、計量、充填などの自動機器に使用する原料の多くは、流動性を向上させるために、前もって造粒します。
②粉末飛散防止
粉体を取り扱うと微粉が飛散し、周辺環境を汚染します。造粒することで、粉立ちを防止できます。
③偏析の防止
粉は、密度、大きさ、形状の違いにより偏りが生じ、製品中の成分含量が不均一になります。複数の原料を一緒に造粒することで、各成分を所定量含んだ粒子が得られ、偏析が防止できます。
④付着の防止
微粉は凝集性が高いため、装置壁面に付着したり、配管内で閉塞したりするので、トラブルの原因になります。造粒することでこうしたトラブルを防ぐことができます。
⑤溶解性の向上
粒は粉と同様に、溶液との接触面積が大きいのですが、粉のように「ままこ」にならないので、溶解性に優れています。
⑥外観の向上
造粒製品は適度な大きさの粒からなり、粒径が比較的均一なので、外観が美しいことが多く、商品価値の向上が期待されます。
(2)コーティングの目的
コーティングの目的は主に次の5つです。
①耐候性の向上
粒子や錠剤の表面をコーティングすることにより、光、酸素、湿気などによる製品の変質や劣化を防止します。
②美観の付与
下地を隠蔽したり着色したりすることで商品価値が向上します。
③苦味、異臭のマスキング
苦みのある医薬品を飲みやすくできます。また、口腔内崩壊錠に含まれる苦味成分を微粒子コーティングすることで、錠剤が口腔内で崩壊しても苦みを感じなくなります。
④主薬間の相互作用防止
反応性のある複数の薬物顆粒を同じカプセルに配合する際に、それぞれの薬物顆粒をコーティングすることで、保存期間中の薬物相互作用を防止できます。
⑤体内における薬物放出制御
製剤に徐放性や腸溶性の機能を付与します。
1.3 造粒メカニズムの分類
造粒のメカニズムは次の3種類に分けられます。
(1)凝集造粒
粒子同士の凝集により粒径が増大する造粒法で、流動層造粒、撹拌造粒、転動造粒などがあります。
当社製品では、流動層造粒乾燥装置 フローコーター(FL)、転動流動層造粒装置 スパイラフロー(SFC)、連続造粒装置 グラニュフォーマー(GF)、遠心転動造粒装置 グラニュレックス(GX)、撹拌造粒装置 グラニュマイスト(GM)、遠心転動造粒装置 CFグラニュレーター(CF)が該当します。
(2)強制造粒
機械的な力により、原料を圧縮成形および/または破砕する造粒法で、圧縮造粒、破砕造粒、押出造粒などがあります。
当社製品では、乾式造粒装置 ローラーコンパクター(TF,FT,FP)、湿式・乾式整粒装置 ミルマイスト(MM)が該当します。
(3)熱利用造粒
噴霧液滴の溶媒蒸発や溶融物質の冷却固化などによる造粒法で、溶融造粒、噴霧造粒などがあります。
当社のシームレスミニカプセル製造装置 スフェレックス(SPX)も熱利用造粒と言えます。
塊状物の破砕により粒子を造る破砕造粒装置を除けば、ほとんどの造粒装置は粒径増大法(Size enlargement)に該当します。
2.1 造粒の目的
製剤工程で造粒操作が行われる剤形として、散剤(細粒剤)・顆粒剤およびカプセル剤が頭に浮かびます。これらの剤形では、形状の付与が造粒の目的と考えられますが、製剤工程における造粒操作の大部分は、錠剤の製造工程で使用されます。通常の打錠工程では、原料粉体の飛散や偏析の防止、高速計量性の確保のため、前処理として原料粉体を造粒します。
厚生労働省「薬事工業生産動態統計調査」医薬品剤型分類別生産金額の推移を、図2と図3に示します。
近年、バイオ医薬品の台頭で注射液剤が増加していますが、それでも錠剤の生産金額は医薬品全体の40%を超えています。
一般に、錠剤の薬価は他の剤形より安価なので、生産量ではさらに高い比率と考えられます。
(残念ながら、厚生労働省の統計では生産金額は開示されていますが、生産量は示されていません。錠剤生産金額の減少は、薬価が安いジェネリック医薬品が普及したことで生産金額の減少につながったように思われます。また、2019年から生産金額が大幅に増加したのは、オンライン報告を原則とするなどの調査方法の見直しが影響した可能性があります。)
2.2 製造方法の選択
安定した打錠操作を行うために、粉末原料を流動性の良い顆粒にしますが、その製造方法は次の3種類に分類されます。
(1)湿式造粒
最も広く用いられているのは湿式造粒です。1950年代には押出造粒(バスケット型)が(他に適当な造粒方法がなかったので)多用されていましたが、1960年代になると撹拌造粒装置が開発され、広く使われるようになりました。その後、国内では流動層造粒で製造した錠剤は、硬度が高く崩壊が速いという特長があり、流動層造粒が最も打錠に適していると評価され、流動層造粒装置が多用されています。しかし、流動層造粒装置は操作因子が多く、外気の影響もうけることから、欧米では撹拌造粒装置が主流を占めています。
(2)乾式造粒
ローラーコンパクターでフレークを作製し、整粒することで打錠用顆粒を得ることができます。ローラーコンパクターで一度圧縮しているので、硬度の高い造粒物が得られます。一方で、圧縮しろ(粒子内空隙)が小さいので、打錠した時の錠剤硬度が高くなりづらい傾向があります。主薬の物性によっては多量の添加剤を加えないと造粒できない原料もあり、国内ではあまり採用されていませんが、湿式造粒に向かない(水分を敬遠する)一部の生薬や抗生物質の造粒に使用されています。湿式造粒に比べ原料を濡らして乾燥するといった工程がないので、製造コストが安く、米国の製薬会社で選択されることが増加しています。
(3)直接打錠(直打)
あらかじめ造粒された添加剤(当社のダイラクトーズ®やグラニュトール®など)と主薬を混合することで、主薬を造粒することなく打錠でき、この方法は直接打錠と呼ばれます。造粒設備や造粒工程が不要になるので製造コストは安くなり、欧米の製薬会社では打錠前処理工程の第一選択になりつつありますが、直接打錠が難しい薬物も少なくありません。
直接打錠に不向きな製剤としては、主に次が挙げられます。
①主薬含有量が多く、主薬の流動性が悪い製剤
②造粒添加剤との混合性が悪い製剤
③主薬と添加剤が偏析しやすい製剤
↓↓↓ 更に詳しく学びたい方へ資料をご準備しております。下記よりダウンロード可能です ↓↓↓
凝集造粒と乾燥の理論的根拠を知ることは、流動層造粒装置や撹拌造粒装置のハンドリング、時間、経費等の管理に有用です。
凝集造粒にはバインダー(結合液)を必要とすることが多く、装置によって加液方法や液量は異なりますが、いずれの場合も造粒と乾燥の基礎理論を知った上で操作されることが望まれます。
操作方法によって造粒と乾燥の時間を短縮することや、ある条件下で起こるトラブルを回避することも可能です。
また、食品の場合は熱や水分で変質や色むらが発生する、メイラード反応で褐変する、あるいは熱軟化するなど敏感な成分が多いので造粒方法や乾燥条件の設定には十分な注意が必要になります。
ここでは、現場で作業するひとりひとりに知って欲しい基礎理論を紹介します。
3.1 固-液系充填構造
粒子-水系の充填構造は水分の増加に従い、無水(Dry)→ 懸垂水(Pendular)→ 索状水Ⅰ(FunicularⅠ)→ 索状水Ⅱ(FunicularⅡ)→ 毛管水(Capillary)→ スラリー(Slurry)と移行していきます。
FunicularⅡとCapillaryの境は、粉体の触感がパサパサ状からネバネバ状に移行する点で、「塑性限界(可塑限界)」(Plastic Limit、PL)と呼ばれ、CapillaryとSlurryの境は粉体の触感がネバネバ状からドロドロ状になる点で「液性限界」(Liquid Limit、LL)と呼ばれています。
図4は、「梅屋の表」と呼ばれるもので、固体(粒子)・液体(水)・気体(空気)の充てん状態を説明する表で、多くの図書(たとえば粉体工学便覧、造粒便覧など)に記載されています1)。
流動層造粒では材料の性質により、次のように造粒時の充てん域(粉体原料内の水分量)が異なります2,3)。
① 吸湿性材料:ペンデュラー域
② 親水性材料:ファニキュラーⅠ域
③ 疎水性材料:ファニキュラーⅡ域
撹拌造粒ではペンデュラー域からファニュキュラーⅠ域くらいで造粒します。
3.2 凝集造粒のメカニズム
図5は液体架橋による凝集モデルです。粉と粉との間に液体が介在すると、そこに液体架橋が形成されます。このとき、液膜内に負圧吸引力と液膜の表面張力が働きます。
乾いた造粒物を得るには、液体架橋を乾燥し固体架橋に変化させることになりますが、そのためには液体中に固体架橋を形成する物質(バインダー)が必要です。
バインダーは原料粒子とは別の物質(たとえばHPC:ヒドロキシプロピルセルロース)を液体中に添加する場合が多いのですが、原料物質そのものが液体に溶けバインダーとして機能することもあります。
バインダーの結合力が小さいと、濡れている間は凝集していますが、乾燥すると一次粒子に戻ってしまいます。したがって、造粒を考えるとき液体架橋の形成だけでなく、固体架橋の形成(=乾燥プロセス)が重要な要素になります。
3.3 乾燥プロセス
造粒が終了すると、乾燥工程に移りますが、湿潤粒子の品温と水分の乾燥の過程は図6のようになります。また、乾燥時間の経過と乾燥速度の変化を図7の乾燥特性曲線に示します。
予熱期間では、粒子表面の水の温度(品温≒排気温度)が徐々に上昇し、一定の温度(熱風の湿球温度)に達します。
この期間の含水率は徐々に減少します。
次に乾燥速度が一定の状態を保つ現象が続きますが、この段階を恒率乾燥期間と呼びます。恒率乾燥期間では、加えられた熱量(受熱量)はすべて水分蒸発のみに費やされます。この期間の乾燥速度が最も速く、このときの品温は熱風の湿球温度を保ち続けます。
このときの湿潤粒子内面のイメージを図8に示します。
恒率乾燥期間は湿潤粒子表面に自由水が存在し、そこで蒸発が生じている間は恒率乾燥期間が続きます。
恒率乾燥期間が終了すると、乾燥速度が遅くなる一方で、品温がしだいに上昇していく段階に移行します。この段階が減率乾燥期間です。
このときの湿潤粒子内面のイメージを図9に示します。この期間では粒子表面の水の蒸発速度よりも、粒子内部から粒子表面への水の移動速度が遅くなります(粒子内部の水の移動速度が律速になります)。
したがって、粒子表面の水分量が低下し、受熱量が水の蒸発に使われるだけでなく、粒子の品温や排気温度の上昇に費やされます。つまり粒子表面が乾き始めたことを意味しています。
恒率乾燥期間から減率乾燥期間に移る点は、「限界含水率」(Critical Moisture Content)といわれます。また、いくら時間が経過してもそれ以上水分が減少しない点が存在します。これを「平衡含水率」(Equilibrium Moisture Content)と呼びます。
参考文献
1)梅屋薫:材料試験,7,298(1958)
2)造粒便覧:P264,オーム社(1975)
3)粉体工学ハンドブック:P377,朝倉書店(2014)
第2章は、錠剤の製造工程で特に重要な、造粒と乾燥についてお送りしました。
最後までお読み頂きありがとうございました。
次回以降、第3章は流動層造粒装置(ハード)、第4章は流動層造粒技術(ソフト)と、2回に分けて流動層造粒についてお伝えして参ります。
このコンテンツが製薬業界の更なる進歩発展の一助となれますよう、心を込めて執筆いたします。
次回もお付き合いくださいますよう、よろしくお願い申し上げます。
↓↓↓ 更に詳しく学びたい方へ資料をご準備しております。下記よりダウンロード可能です ↓↓↓
※上記、記事中の物と同一のダウンロード資料です。
キーワード: