10 reasons why our screen type classifier “TURBO-SCREENER” continues to be preferred choice Machinery 2024.06.25
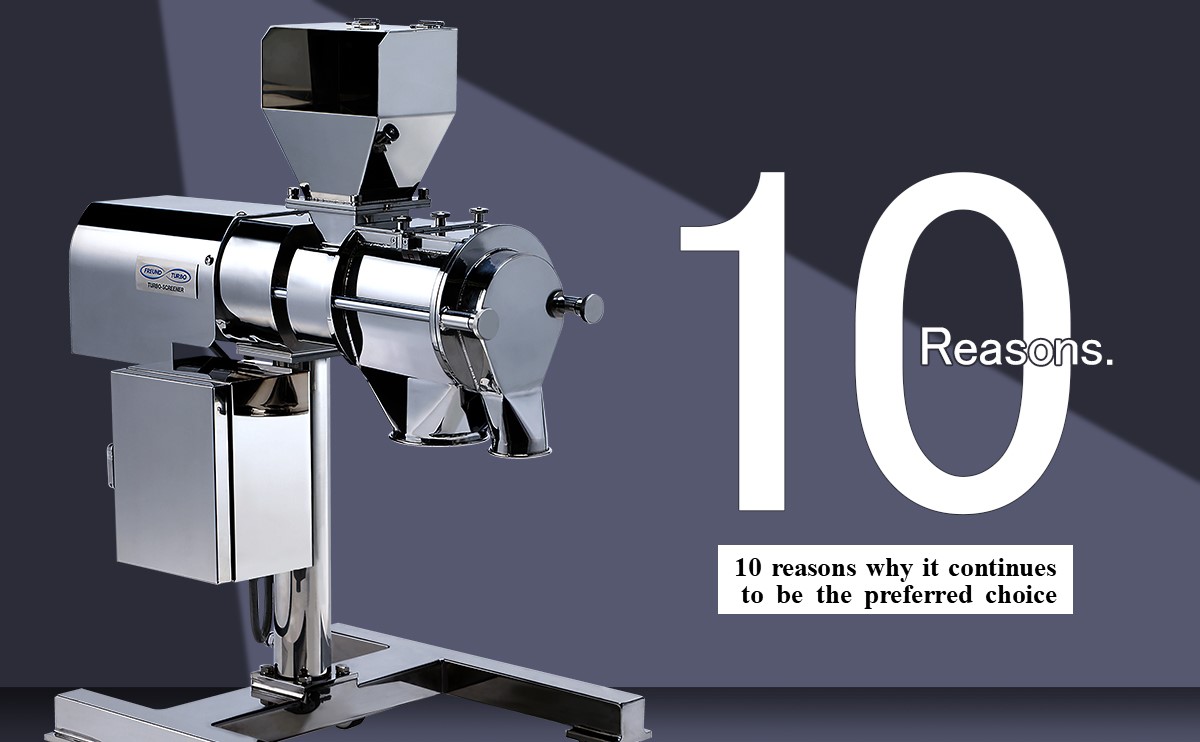
Thank you for viewing FREUND KNOWLEDGE OCEAN.
My name is Toshiya Komagata and I am from the Testing Section, Development Division, FREUND-TURBO CORPORATION*.
This article introduces our original screen type classifier “TURBO-SCREENER” that still continues to be the preferred choice by our customers after more than 40 years since its release.
If you are having trouble removing fibrous foreign substances or with clogging with a vibrating sieve, or if you are concerned with the classification performance of air classifiers or loss of raw materials, please consider our TURBO-SCREENER as the perfect choice for your future equipment upgrade.
At the bottom of this article, you can download technical data for engineers who are engaged in classification that describes evaluation methods for classification tests, etc. Please read through the following in its entirety.
* On June 1, 2024, our company logo was changed to the FREUND Group’s global logo. The company logo in the images of this article is our old company logo.
Komagata Toshiya
Development Division, FREUND-TURBO CORPORATION.
After joining FREUND-TURBO CORPORATION, he was in charge of contract grinding operations in the Pulverizing Section.
In 2014, He was transferred to the Testing Section and engaged in assembly, running, washing, etc., of testing equipment.
Currently, He is in charge of testing TURBO-SCREENER and conduct around 100 test cases per year.
TURBO-SCREENER is a classifier that can efficiently and continuously sieve powdery raw materials with a high yield by rotating the rotor blades at high speed inside the resin-made cylindrical screen.
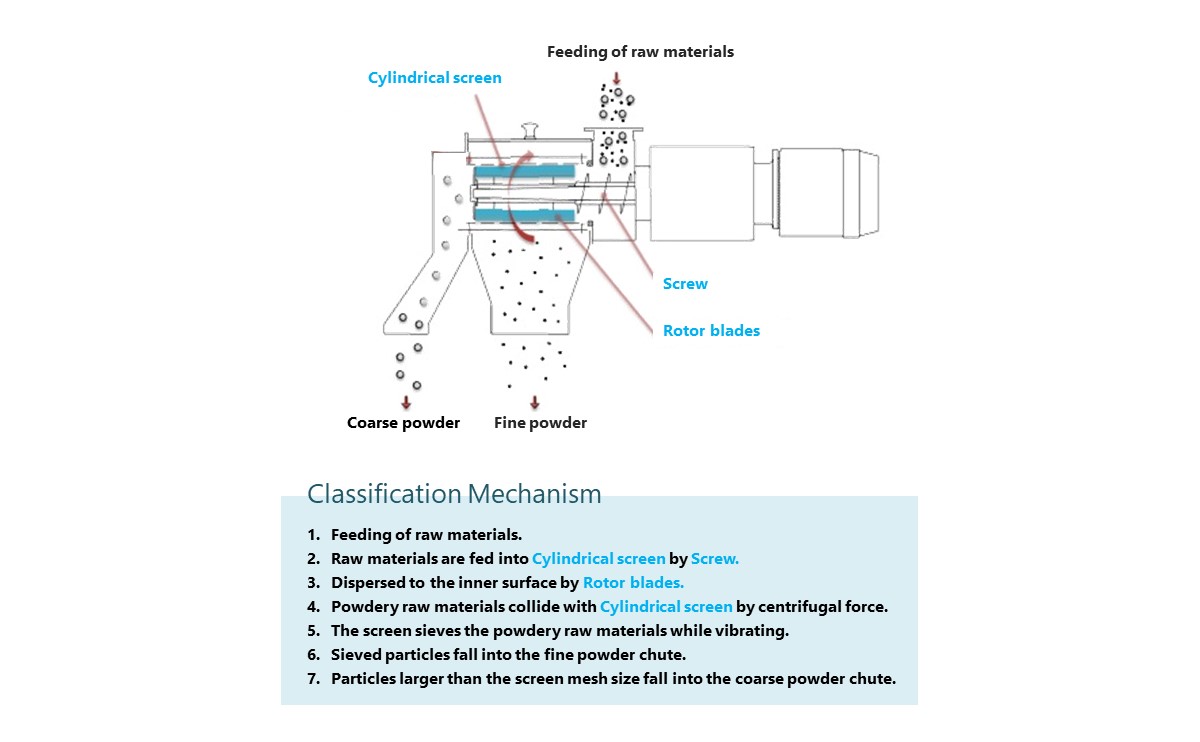
The greatest feature is that it effectively utilizes the “screen vibration” generated by the raw materials agitated by the high-speed rotation of the rotor blades. Large amounts of materials that are hard to classify with vibrating sieves or air classifiers, such as powder high in aggregability / adherability and powder having a very small bulk specific gravity, can be sieved in a short time without clogging.
Metallic-screen plane type vibrating sieves made up the vast majority of the classifier market around 1980, but TURBO-SCREENER we developed proved easy to operate and maintain and, at the same time, offered excellent disassembly and washing properties due to its simple structure. Even now, after more than 40 years since its release, it continues to receive high praise and approval and is used by many customers.
The following are 10 reasons why TURBO-SCREENER has been highly valued for more than 40 years since its release.
(1) Fibrous foreign substance removal performance
Due to the centrifugal force exerted by the rotation of the rotor blades, hair and other fibrous foreign substances are hardly oriented vertically to the screen mesh, and are discharged together with coarse powder in a short time.
For the reasons stated above, TURBO-SCREENER is highly valued for removal of hair and other fibrous foreign substances, which vibrating sieves prove insufficient in handling, and offers a record of performance in deliveries to the pharmaceutical and food industries.
(2) High classification performance
The screen set inside TURBO-SCREENER generates continuous vibration due to the impact of the raw materials agitated by the rotor blades rotating at high speed. The vibration enables continuous sieving while automatically eliminating clogging (self-cleaning).
Therefore, raw material powder high in adherability and aggregability, which general vibrating sieves prove insufficient in handling, as well as spherical particles, can also be classified without clogging.
(3) High processing capacity
Since the raw materials fed into TURBO-SCREENER are dispersed over the entire screen due to the high-speed rotation of the rotor blades, they can be efficiently classified by using the entire screen.
Also, since the materials are subjected to centrifugal force and collide with the screen, a large force is exerted to pass them through the screen, forcing them to be classified.
Furthermore, due to an increased number of contacts between the raw material powder and screen, there are more chances for the materials to pass through the screen. In other words, an extremely high processing capacity can be obtained by the synergy between “use of the entire screen,” “forced classification by centrifugal force,” and “the number of contacts with the screen.”
Compared with a general vibrating sieve having the same screen area, it has more than five times the processing capacity.
(4) Agglomerates can also be deagglomerated
The raw material powder fed into TURBO-SCREENER, even when in an agglomerated state (to such an extent that they can be lightly loosened with fingers), is continuously sieved while being deagglomerated due to the impact by contact with the rotor blades rotating at high speed and the impact by colliding with the screen as they are agitated. Therefore, significant yield enhancement will result.
In addition, even such powder high in adherability / aggregability that would gradually be granulated on the mesh of a vibrating sieve (titanium oxide, nickel oxide, lactose, buckwheat flour, wheat flour, etc.,) can also be instantaneously classified because it is powerfully agitated and dispersed in the screen.
(5) Raw materials having a small bulk specific gravity can also be processed
On vibrating sieves or ultrasonic sieves, the force exerted when raw materials come in contact with and pass through the screen is largely dependent on the raw materials’ own weight; therefore, raw materials having a small bulk density (e.g. 0.1g/cc) are hard to pass through the screen and difficult to classify in many cases.
In contrast, TURBO-SCREENER can classify even raw materials having a small bulk density (such as light anhydrous silicic acid) because the raw materials subjected to a centrifugal force by the high-speed rotation of the rotor blades are forced to collide with the screen. Moreover, by controlling the rotational speed of the rotor blades, optimum classification conditions can be set according to the bulk specific gravity of raw material powder.
(6) Excellent maintainability
The basic structure of TURBO-SCREENER is simple as each part is inserted and then bolted to the guide rod on the side of the main body. It can be easily disassembled and reassembled by one operator in five minutes, and the only part that requires a tool is the “one bolt” at the shaft end.
Furthermore, all the removed parts can be washed, and TURBO-SCREENER is structurally error-free during reassembly, and together with just a small number of parts, it offers exceptional maintainability.
The resin-made screen is set in the machine as a unit attached to a SUS (stainless steel) frame. Therefore, if a screen unit is prepared in advance, replacement can be completed in approximately one minute by simply replacing the unit. Since it takes little time to replace the screen, machine shutdown time can be shortened considerably, which improves production efficiency.
It is also easy for an operator to attach a resin screen to a SUS frame, which requires approximately 10 minutes, and there is no need to return the screen to the manufacturer for replacement. One of the major advantages of using a tension gauge is that there is little variation between operators, and the setting can always be performed under the same conditions.
* Please press Shift+F5 to clear your browser cache if the video does not appear.
(8) Improvement of the working environment (quietness / prevention of dust generation)
Such problems as vibration and noise arise with general vibrating sieves, which perform classification by vibrating a huge drive section that makes up a large part of the equipment structurally. In contrast, TURBO-SCREENER has a structure in which classification is performed by the rotational motion of the drive section, so it has far less noise and vibration than a vibrating sieve.
Also, connecting the feed port and discharge port with a ferrule, flexible tube, or the like enables highly airtight classification, and due to the high airtightness, dust generation in a workroom can be suppressed, with the result that the working environment can be improved for a cleaner workplace.
(9) Only a volumetric feeder is needed as auxiliary equipment
The number one reason why TURBO-SCREENER demonstrates such high performance is that it “effectively utilizes screen vibration for classification.”
By feeding raw material powder with use of a volumetric feeder such as a vibrating feeder or screw feeder, stable and satisfactory screen vibration can be obtained and high classification performance and processing capacity can be achieved. Since the raw material powder is fed by free-falling and also discharged by free-falling after being classified in the screener, there is no need for other auxiliary equipment, such as a cyclone and blower.
(10) Classifiable even with the mesh size 50μm or less
Generally, when classifying powder using a screen, the smaller the primary particle size of the raw materials, the more it is affected by adherability / aggregability, making classification more difficult.
In contrast, TURBO-SCREENER is capable of classification even with a fine mesh size of 50μm or less because the raw materials are subjected to centrifugal force by the high-speed rotation of the rotor blades forcing them to collide with the screen, and the impact, exceeding the effects of adherability / aggregability, acts as a force so that they pass through the screen.
TURBO-SCREENER has been widely used in pharmaceuticals, foods, cosmetics, and chemicals, offers examples of classification with diverse raw materials.
The following is just one example of classification related to pharmaceuticals.
For customers who are concerned about metallic contamination, the only countermeasure was to coat the powder contact areas, but there were still concerns that fitting parts and threaded portions, etc., could not be coated and peeling was a also a concern.
Therefore, as a more reliable countermeasure, all parts in the powder contact areas have been made of resin. The features are as follows:
1. Complete prevention of metals from being mixed in by abrasion, etc.
“We do not permit any metals to be mixed in. We strive to limit this to the absolute minimum.”
This all-resin specification for powder contact areas proves ideal for such customers.
As the name suggests, by using resin for all parts in the path that come into contact with raw materials, we have minimized the risk of metallic contamination caused by collisions and friction.
2. For raw materials high in metal corrosiveness
By using resin high in corrosion resistance and chemical resistance, it is now possible to sieve chlorides and strong base raw materials, which metals prove insufficient in handling.
3. Improvement of maintainability and handling performance by weight reduction
Parts made of resin have realized significant weight reduction.
Even parts exceeding 20kg in standard specifications (made of SUS) can be reduced to 5kg or less in weight when made of resin. This contributes to reducing the burden on operators and improving safety measures during disassembly, washing, and maintenance.
4. Compatibility with delivered machines (made of SUS as standard)
TURBO-SCREENER that are currently in operation can also be changed to resin specifications by replacing the relevant parts. Simple replacement of the target parts in the powder contact areas, as the motor and drive mechanism are left as they are, enables a change to resin specifications. There is no need for additional work. As a matter of course, resin specifications can also be changed to standard specifications (made of SUS).
Machines made of SUS and of resin can also be purposed for multi-use according to raw materials and production conditions.
The above are 10 reasons why the screen type classifier TURBO-SCREENER we manufacture and sell has been highly valued for more than 40 years, and the introduction to the all-resin specification for powder contact areas that limits the risk of metallic contamination to the absolute minimum.
You can test TURBO-SCREENER on an actual machine at the head office of FREUND-TURBO CORPORATION in Yokosuka city, Kanagawa, Japan.
If you are having trouble removing fibrous foreign substances or with clogging with a vibrating sieve, or if you are concerned with the classification performance of air classifiers or loss of raw materials, please feel free to contact us.
In addition, you can download technical data for engineers who are engaged in classification from the link below. We hope you will find this data useful.
Thank you very much for reading through this article.
Please feel free to contact us using the inquiry form below if you have any questions or would like to request a trial test.
KEYWORD:
- SHARE
- Share
- Post
- Send to LINE
- Send to Mail