【導入事例】田辺三菱製薬×三菱ケミカルエンジニアリング×フロイント産業による、医薬品の連続生産システム 機械 2022.06.20
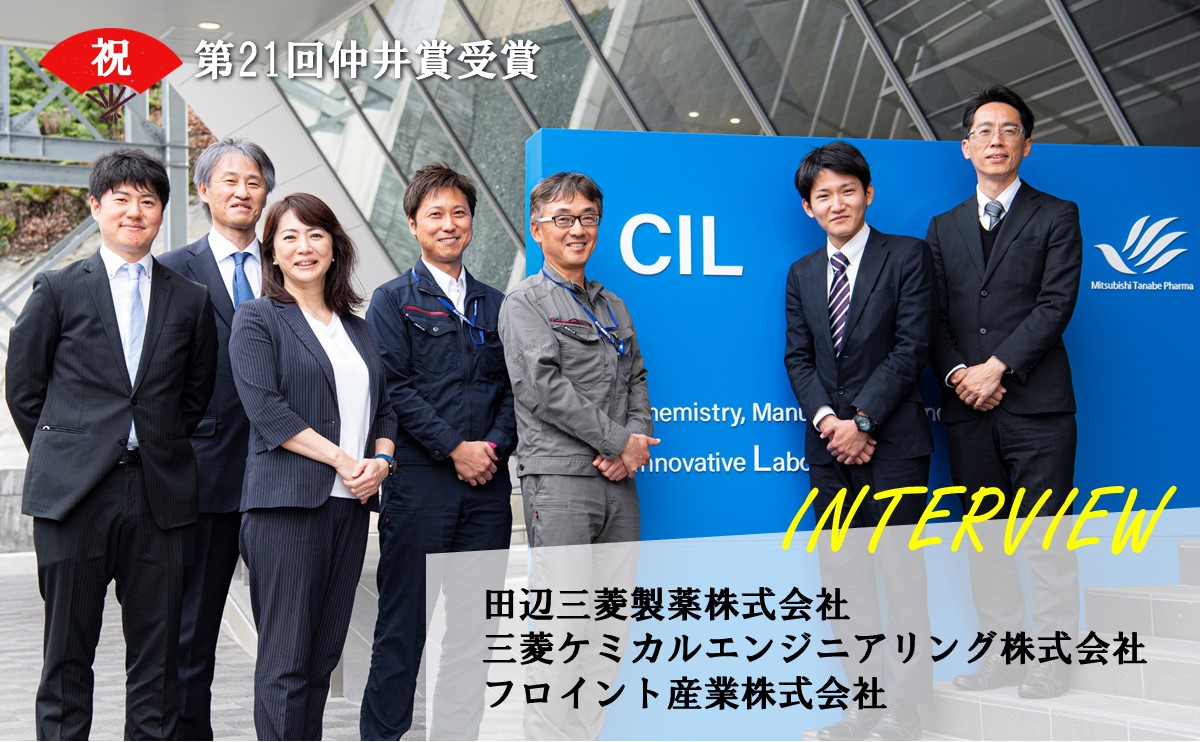
いつもFREUND KNOWLEDGE OCEANをご覧頂き誠にありがとうございます。
フロイント産業CS戦略企画部の山口です。
今回は、「固形製剤の連続生産システム構築に向けた取り組み」により2021年、第21回仲井賞※を受賞された田辺三菱製薬株式会社様と三菱ケミカルエンジニアリング株式会社様にお話を伺って参りました。
医薬品連続生産システム導入の背景から、プロジェクトの歩みと当社の湿式連続生産装置Granuformer選定の決め手。更に導入時の課題やその解決方法、今後の医薬品業界の展望まで幅広くお聞きしておりますので、是非最後までお読みいただければ幸いです。
※仲井賞:一般社団法人製剤機械技術学会が、製剤機械技術の進歩と発展に貢献した個人又はグループに顕彰している賞のこと
詳細は下記リンクをご覧ください
1933年設立
MISSION:病と向き合うすべての人に、希望ある選択肢を。
VISION 30:一人ひとりに最適な医療を届けるヘルスケアカンパニー
1957年設立
企業理念:英知を集めて、新しい価値を創造し、広く社会に貢献する。
スローガン:Better Engineering for Well-being
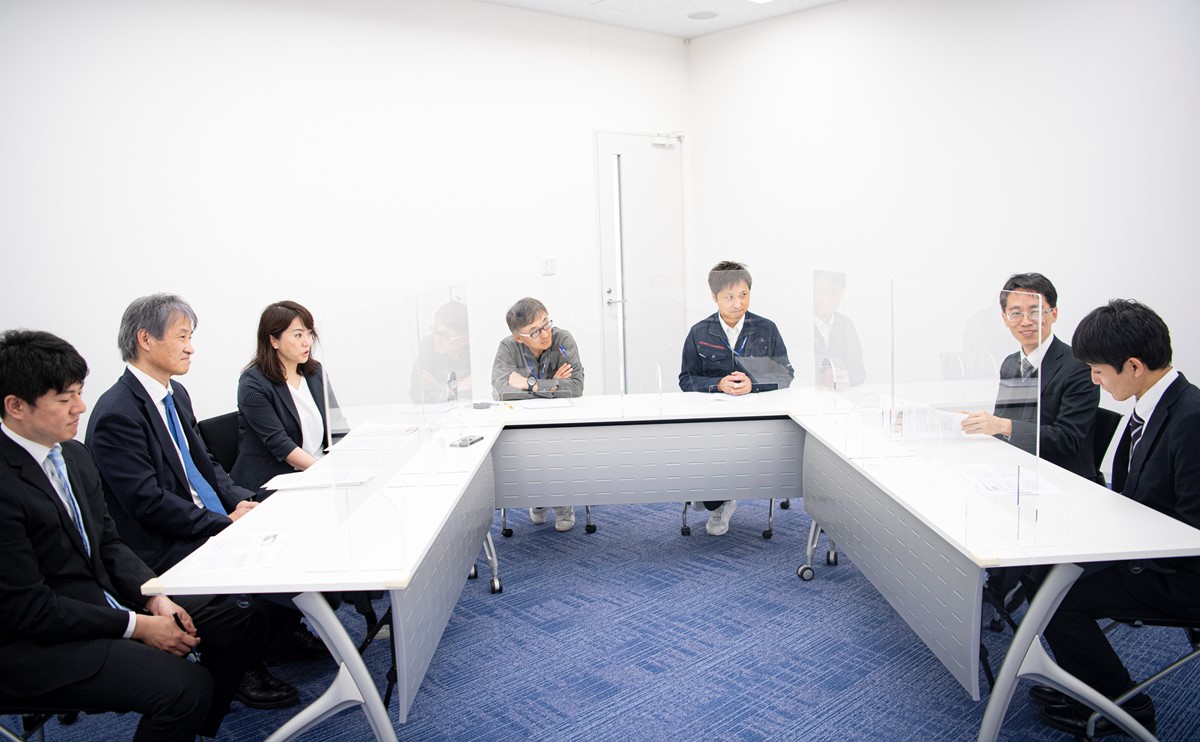
(左から)
フロイント産業株式会社 開発担当 菅野
フロイント産業株式会社 技術開発研究所所長 鵜野澤
フロイント産業株式会社 インタビュアー 山口
田辺三菱製薬株式会社 サプライチェーン本部 製品技術研究所長 杉本様
田辺三菱製薬株式会社 同研究所 製剤研究3Gマネジャー 今田様
三菱ケミカルエンジニアリング株式会社 解析Gマネージャー 田中様
三菱ケミカルエンジニアリング株式会社 解析グループ 村田様
※本文中は、田辺三菱製薬株式会社 杉本様・今田様を(水色)、三菱ケミカルエンジニアリング株式会社 田中様・村田様を(緑)で記載させていただきます。
※また本文中一部、田辺三菱製薬株式会社様を(MTPC)、三菱ケミカルエンジニアリング株式会社様を(MEC)と記載させていただきます。
山口:この度は第21回製剤機械技術学会仲井賞の受賞おめでとうございます。
医薬品業界の発展にご尽力されました貴社の功績が認められ、私どもにとりましても喜ばしい限りです。その後、皆様のご活躍におかれましては、社内外関わらず何か反響はございますか?
杉本:社内イントラに掲載されたことで、仲間から「すごいですね」という声をかけてもらったり、他部署からも嬉しいという言葉をもらえました。
社外では同じ業界の方々から、そこまでやっていたんですかとも言っていただきました。
田中:当社も社内報に掲載されました。盾を持ったにこやかな写真を広報部に撮ってもらい、社内で認知され始めたところです。
村田:社内報のお陰で社内の認知が増え、同僚から「受賞したんや」という声掛けもありました。なかなか業務を通じて盾をもらえることはないので、非常に嬉しい出来事でした。
山口:ここからは、連続生産システムの導入について具体的にお伺いします。はじめに導入を検討された背景、理由などを教えていただけますか?
今田:これまで当社は医薬品を安定的に製造していたので大きな課題にならず、連続生産への取り組みや設備投資は後回しになりがちでした。しかし外部環境が変わり、より早く治験薬を市場に届けたいと思い、スケールアップが不要であり、製造量を自由にコントロールできる点に注目し、連続生産システムの検討を始めました。
山口:外部環境は、具体的にどのように変わったのでしょうか?
今田:製薬会社の使命として、いかに早く患者さんに薬を届けるかを前提に日々の活動に取組んで参りましたが、開発着手から、臨床試験→承認申請→商用化に向けた活動に関して、この流れはどんどん早くなっています。当社でも、開発期間をいかに効率化してスピードアップさせるか、また流通部分も含め、省エネ・無駄の削減も強く意識するようになりました。
山口:そのスピードアップは、製薬会社の努力で達成できるものなのですね。
杉本:開発の初期段階は、例えばスケールを1g、10gというところから作りはじめ、実際の生産段階では数100kg単位で作ります。一般的に医薬品の製造においては、装置のスケールに合わせて1kg、10kg、100kgと結果を積み上げ、製造販売の承認取得へと向かいます。これらの期間を詰める努力を行い、スピードアップを図っています。連続生産技術を導入することで、製造条件(デザインスペース)の構築が容易になりますと同時に生産設備へのスケールアップの省力化・検討期間のスピードアップが容易になります。
連続生産技術の導入はスピードだけでなくコスト的にもメリットがあります。
山口:ありがとうございます。三菱ケミカルエンジニアリング様での連続生産システム導入の背景も教えていただけますか?
田中:三菱ケミカルエンジニアリング株式会社という名前の通り、親会社は三菱ケミカルホールディングス社で、もともと石油化学、石油生成、それに派生する石油製品をたくさん作っている工場を持つメーカーです。当社はそのようなプラントを建設する仕事をしてきました。石油化学は原料を入れ、そこから途切れることなく連続で製品を作るものが非常に多く、途中で原料を取り出すことなくプロセスが進みます。
石油化学での連続生産の知見があり、他業界にも貢献したいという想いがありましたので、今回のケースでは両社の想いがマッチしました。
また、まだ世の中にないことにチャレンジしていくことも、当社にとって戦略上の重要な活動のひとつであり、経営層にも理解を得られました。
山口:仲井賞受賞理由の中に、田辺三菱製薬様の「製剤技術」と三菱ケミカルエンジニアリング様の「エンジニアリング技術」の連携・融合を成し遂げた、とありました。同じ三菱ケミカルホールディングスグループでありながら、これまでは協業されることはなかったようですが、どのようなきっかけで今回初めて実現したのでしょうか。
今田:お互いに課題を持っていたところ、たまたま学会で出会いました。
杉本:三菱ケミカルホールディングスという同じグループであり、グループ内での協業につき、いくつかのテーマで議論をしてきましたが、ゴールまで辿りつける案件はあまりありませんでした。
そんな時に、たまたまISPE日本本部※で、連続生産関連のセミナーがあり、そこで話し合う機会を得ました。石油化学と医薬品では、なかなか協業のイメージが湧かなかったのですが、対話を重ねていく中で医薬品製造における連続生産という視点での協業の可能性に気づくことが出来ました。接点を見つけるきっかけが重要だなと今、改めて思いました。
山口:石油化学業界では連続生産が当たり前。製薬業界ではトレンドだった。ということですが、MECさんとして製薬業界で初めて連続生産にチャレンジすると聞かれた時、どのような印象を持たれましたか?
村田:「いよいよ、われわれの培った技術を他業界で活かせるのか。やってやろう!」という気持ちになりました。(笑)
杉本:実験が上手くいかない時にはMECさんのシミュレーションデータを用いて改善できるので、非常に良いコラボだったと感じています。
鵜野澤:その通りですね。われわれは装置メーカーなので、課題が発生した時に該当箇所の設計や構造変更を行うことは得意です。どこをどう改善したら良いかについて、過去の経験および実装してからの結果(データ)に基づいて対応します。MTPCさんへの設備導入時の課題に、MECさんのコンピュータシミュレーション技術が活き、速やかに解決へと進みました。
当社といたしましても、2社の協業に立ち会う機会をいただけたことは大変な幸運でしたし、そのノウハウが蓄積され、財産になりました。
※ISPE(International Society for Pharmaceutical Engineering, Inc.):国際製薬技術協会
詳細は下記リンクをご覧ください
山口:村田さんが一番ご苦労されたことは何ですか?
村田:Granuformer(グラニュフォーマー)の乾燥部で発生した課題があげられます。具体的には配管内壁への粉体付着です。これは内壁面全体へ付着するような現象ではありません。配管経路の途中に生じた局部的な付着の発生です。付着品が経時的に脱落して製品に混入することは、たとえ万に一つの確率であっても防止しなければならないと考えました。その解決にあたり、当社のコンピュータシミュレーション技術を活用して、データ解析と対策検討を重ねました。フロイント産業の浜松事業所にも訪問し、データ解析で得た結果を反映し、配管のこの部品をこのように作ってほしいという要望を伝えると、軽快なフットワークですぐに対応してもらえました。机上で検討しても分からないことは多々あります。ハード部品の製作を速やかかつ忠実に対応していただいたお陰で、当社のシミュレーション技術が活きました。すぐに実装実験ができ、フィットするか否か、どこに微調整が必要なのかの確認も迅速に行えました。
菅野:われわれも、「配管にどのくらいの必要空気量を供給すれば粉体の付着が解消するか」を追求するにあたり、MECさんのシミュレーションデータで対策案を絞っていただけたことにより、非常にスムーズに進められ、大変ありがたかったです。
杉本:10年ほど前からシミュレーション技術を使って何かできないかと検討していましたが、当時は「時間がかかるな」という印象でした。計算に2週間かかるのであれば実験の方が早いかなと。
10年経ち、実用性が上がってきたと感じますがいかがですか。
村田:仰る通りで、10年前に比べると格段に計算のリソース、パフォーマンスは上がっていて、計算手法自体も工夫されています。
例えばイメージとして、これまでは縦、横、高さの3次元まで計測を必要としていたものを、横の1次元の計測だけで、それ以外を予測してアウトプットできるように技術が進歩しています。そのため、計算も簡略化させて速度を上げています。今後も実用性の向上に期待して良いと、私は思います。
山口:続いて、連続生産プロジェクト発足の経緯やプロジェクト体制、現在までの歩みを教えていただけますでしょうか
今田:連続生産に関する検討以前から、プロセス分析機器(PAT※)の進歩も感じており、社内で導入を検討していました。QbD※(クオリティ バイ デザイン)が事例として報告されることが多くなり、日本国内でも連続生産の取り組み事例が報告されるようになってきました。そこで2015年ぐらいから当社も取り組む必要があると認識し、具体的な検討を始めました。
田中:われわれ技術屋は、プロジェクトが発足してから参画しました。2016年、連続生産の肝となるのは『造粒』だと考え、「どのメーカーの造粒機を選ぶか」というところから入りました。
飛び込んだ先の課題が、粉を湿らせて練ってもう一度乾燥させるという非常に難しい内容でした。そのため、情報交換やシミュレーションを何度も繰り返し、たくさんのデータも提出してもらい、皆さんと合意して進めることが出来ました。
2年半から3年ぐらいかかった造粒装置の選定に、一番時間を費やしました。
※PAT(Process Analytical Technology):リアルタイムな計測により、医薬品の製造工程の設計、分析、管理を行い、最終的に製品の品質を保証するシステム
下記、公益社団法人日本薬学会ホームページより引用
※QbD(Quality by Design):設計品質。ICH Q8 Annexでは、事前の目標設定に始まり、製品および工程の理解ならびに工程管理に重点をおいた、立証された化学および品質マネジメントに基づく体系的な開発手法(じほう社2022年4月発行、ICH・GXP医薬用語手帳2022を引用)
山口:最終的に、当社のGranuformerを選定して下さった訳ですが、決め手はどんなところでしょうか?
田中:まずはプロジェクトオーナー様の要望通りに造粒できること。その上で故障した際のメンテナンスやサポート体制。そして導入する際のコストも重要です。
われわれが機種を選定する際には色々なポイントがありますが、トータルで一番要望にマッチしていたのがフロイント産業さんでした。
質問に対する技術的な回答も早く、柔軟に対応いただいたことは、選定期間中の会話でもよく分かりました。
山口:ありがとうございます。このように言って下さっていますが、浜松事業所では、何か意識して取り組まれていたのでしょうか?
菅野:私どもは、「顧客満足度をいかに上げていくか」を常に考えており、お客様への早急な回答はとくに意識して対応しています。
鵜野澤:お客様に価値を認められて初めて形になる商品です。対応がスピーディーかと言われると少しくすぐったいところがありますが、そのように仰っていただけることは、非常にありがたいです。
山口:機器の選定は、MECさんが主体となり進められたのでしょうか?
今田:ディスカッションした上で、最終決定は当社が行いました。
製薬会社の目で見ても、造粒乾燥を重要工程と考え、そこに比重を置き選定しました。
色々な機械をテストさせてもらい、このメーカーはこの点が特徴という議論をしました。Granuformerは乾燥工程がユニークで乾燥時間が非常に短いため、最終的に出てきた顆粒がどのような状態かすぐに測定でき、それを受けて運転条件の調節もスピーディーに対応できる点がメリットでした。また、この点が仲井賞受賞のポイントにもなったと思います。
山口:乾燥部分がユニークというのは具体的にはどのようなことでしょうか?
今田:気流式乾燥は一般的な医薬品の製造ではあまり使われていなかった乾燥方式です。造粒物を一度集めてまとめて乾燥させるのではなくて、温風の気流に同伴した粒子をずっと乾燥し続ける。そこが特徴的であり、乾燥の速さに繋がっています。
菅野:乾燥機構は、とくに他社と差別化し、Granuformerのセールスポイントにしている部分でもありますので、その特徴を理解していただけて嬉しいです。乾燥が速いことに加え、常に完成品が出てくるので、仮に品質の逸脱を検出してもその僅かな量を切り取って排除すれば良く、製品ロスの削減にも繋がっています。そこを評価いただいて、選んで下さったのかなと思っています。
今田:品質の逸脱等が見つかったら、すぐに運転条件を修正できるのも良いですね。
鵜野澤:連続生産装置を開発する中で、当社の開発コンセプトとして『どのようなものがお客様に必要とされているか?』を社内で議論し、価値を認めていただける商品を目指してユニークな機構を採用するに至りました。
山口:それでは次に今回の導入において、どのようなハードルがあり、それをどう乗り越えられたか教えていただけますか?
今田:まずは、連続生産設備の上流工程から下流工程まで全てまとめて設備投資するのか、製品の開発状況に合わせて工程ごとに投資していくのか、色々なパターンを検討しました。今回は、工程ごとに評価しながら導入したので、割と社内承認が得られやすかったです。乾燥部分の粉体付着の様に、実際に実験して分かったことも多くあり、それらをMECさんと協力して、シミュレーションを活用しながら解決していくことで乗り越えられたと考えています。
杉本:技術的なハードルという点で1つ印象に残っているのですが、非常に短時間で乾燥されるというユニークなメリットがある反面、乾燥時間を長く出来ないというデメリットもあります。
従来の方法だと、乾燥時間を長くしたり温度を上げることで乾燥できる幅が広がりますが、機器の特性上、今回は数秒と決まっている乾燥時間を延ばせないという制約がありました。
乾燥が思った通りにならなかった時には、シミュレーション結果を基に適切に配管の構成を変えてもらったこともありました。
機械メーカーからすると、こちらの要望通り全て改良していたらキリがないと思います。
双方で話し合い、テストを繰り返して一つひとつのハードルを越えていきましたが、短期間でここまでやります!と言って実際に対応してもらえたことは良い思い出です。
村田:最初の設計では、乾燥後の原料回収率が目標値を下回り、若干量のロスが出ており、回収率の向上というのもハードルでした。
製品回収するサイクロンの部品のパターンを変えるなど、改良と実験を繰り返し、最終的に100%に近い回収率になり、目標を達成しました。
今田:全体の製造から若干量のロスと聞くと少ないように感じるかもしれませんが、主薬含量は錠剤全体の割合でいうと少ないこともあるので、ロス品に主薬が含まれていると、最終評価した際にワーストケースでは主薬が残っていないということもあり得るのです。そのため、回収率は重要です。
鵜野澤:われわれだけですと特殊な主薬を使っての実験は出来ません。二社協業の一端を当社も担い、三社で検討させていただいたことは、大変よい勉強になりました。
山口:連続生産システムを導入後の現在、どのような取り組み・活用をされていますか?
今田:これまで連続生産設備を段階的に導入してきたので、それらを全て繋げるシステムを構築中です。今、まさに菅野さんにも手伝っていただいています。完成後は、連続生産設備を全て繋げた場合のデータ取りをして課題や傾向を把握し、最終的に生産システムとして成り立たせるために、現在準備をしている状態です。そこまで整ってようやく管理戦略を立てられます。どこでどのパラメーターを測定し、ダメだった時はどこの条件を変えるのか、データを取り決めていく予定です。
山口:現在使用されている中で、何か課題は見つかっていますか?
今田:ないと言えばウソになりますが、どちらかというと機械ではなく処方由来です。まだ開発中という状況ですね。
山口:それでは最後に、今後の展望についても、お聞かせいただけますか?
杉本:製薬業界は、低分子固形製剤、バイオ品、遺伝子治療など、モダリティのトレンドがどんどん変化しています。
また、近未来の姿として「個別化医療」というものも話題になっています。
現在、薬は年齢によって服用量が決められていますが、人によっては多すぎたり少なかったりします。その人に最適な服用量であれば副作用も出ず、しっかりと作用する。
これからはPATや周辺技術の進化で様々な生体情報を瞬時にセンシングできる世の中になると思います。その情報をAIドクターが解析し、自動投薬まで出来れば最適な投薬が実現できるとともに飲み忘れもなくなります。
「広い視野で世の中に何が求められているか」「どんな技術を使えばいいか」を考え、必要な技術の専門会社と協業して、一緒に議論しながら連続生産だけではなく医療に関わるもの全ての可能性を考えていかないといけない。それがわれわれの課題だと考えています。
今田:医薬品メーカーとして、最適な薬剤を最適なタイミングで届ける。かつ安定供給することが使命だと考えています。その中で今回の連続生産システムを考えると、まずは導入したので早くシステムを用いて製品を供給したいです。
「医薬品を少しでも早く届けるようにする」「廃棄物を減らす」「エネルギー量を削減する」ということに繋がれば良いなと思っています。
今までのように、一度に大量生産して供給するのではないフレキシブルな対応。それが連続生産だと実施しやすいと考えています。
田中:われわれはエンジニアリング会社ですので、プロジェクトオーナー様がどういう工場を作りたいか?というところに寄り添い技術を磨いていかないといけない。希望のイメージをしっかり受け止めて、それを具現化できるシステムを提供します。
今回の連続生産システムは先進的で大きな取り組みでした。ここでのノウハウが他でも使えるかもしれないですし、ここで使っていないものも次世代の連続生産システムに役立つかもしれない。という視点で、常に技術を磨いていくしかないと思っています。
山口:田中さんが製薬業界の製造現場をご覧になって、更にシステム化できそうだと感じた部分はありますか?
田中:製薬業界は粉を使用し、われわれは液体を使用しているので、全く原料のハンドリング技術が違います。まだまだ勉強不足で、今回のプロジェクトを通してお客様に起こっている事象を目の当たりにしましたので、粉体技術に関しても提案できるエンジニアリング会社になりたいと考えています。
杉本:田中さんにお聞きしたいのですが、連続生産は自動化に繋がりやすい技術だと思いますが、インダストリー4.0とか、デジタルツインとか、ドイツが先行している流れを日本でも取り入れていくにはどうしたらよいでしょうか?何かお考えはありますか?
田中:DX(デジタルトランスフォーメーション)、デジタルツインにしても、われわれエンジニアリング会社がやりたいというよりは、「お客様がそれを使って何をやりたいか」が大事だと思います。デジタルツインと言えば運転データやセンシングなど、大量のデータを取り込み解析することで、ある程度先の未来を検知するのですが、それなりの期間、運転を続ける必要があります。DXで何をされたいか?どこまでやるのか?を議論し、しっかりと目的を把握した上で形にしていくことがわれわれの仕事だと考えています。
山口:フロイント産業にとっても「デジタル化」は、今後の開発ポイントの一つと考えます。お客様にとってより使いやすい装置となるように、どのように取り入れられるか検討していきたいと思います。皆様、本日は大変貴重なお話をありがとうございました。
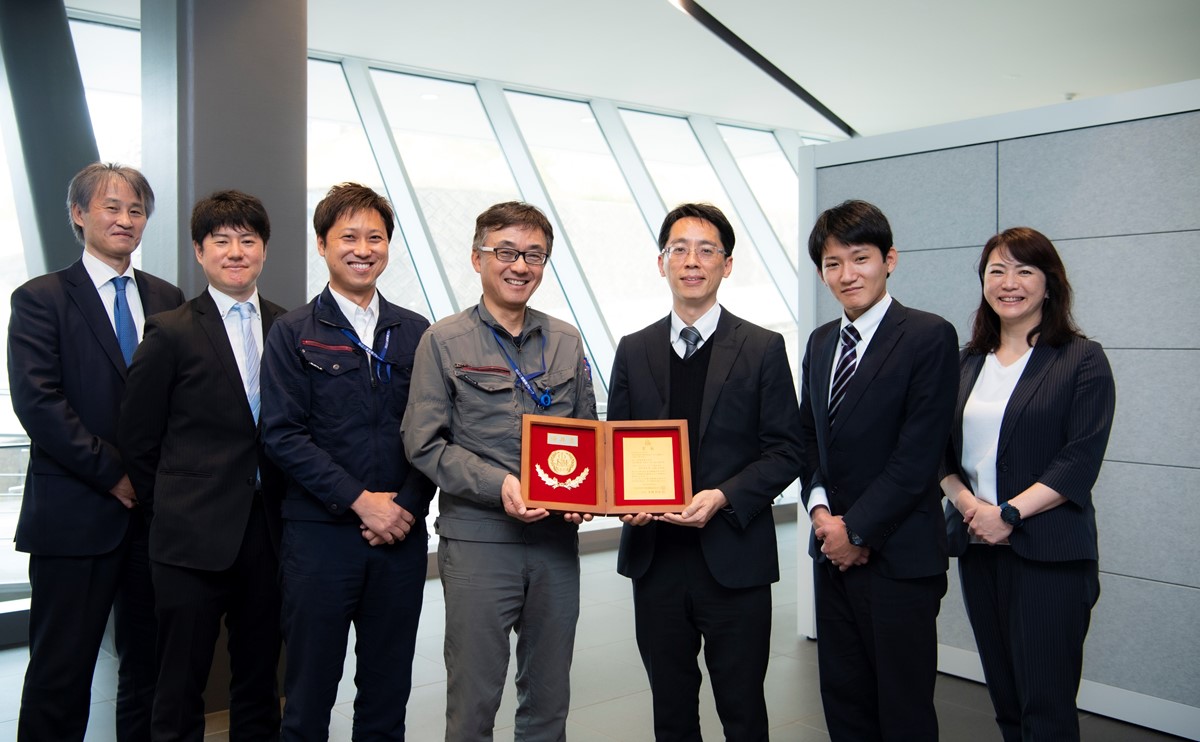
医薬品製造とエンジニアリングという全く異なる事業を営む二社が、協業で「固形製剤の連続生産」という新たなシステムを構築された経緯をお聞きしました。
それぞれの持つ知見と技術が融合し、素晴らしいシナジー効果が生まれました。
田辺三菱製薬様は、まずは既存製品の製造プロセスを造粒から打錠工程まで連続化し、一部変更申請を行われる予定で、その後は開発中の新薬の治験薬製造にも連続生産を応用される予定です。
フロイント産業も「創造力で未来を拓く」の企業理念を胸に、医薬品業界を中心とする様々な業界のお客様のお役に立てる技術を生み出す努力を続けてまいります。
なお、今回の記事中に掲載されております湿式連続生産装置Granuformerの製品詳細については、お気軽に下記よりお問い合わせください。
最後までお読みいただき、ありがとうございました。
キーワード: