覚えておきたい製剤技術の基礎知識! 第3章:流動層造粒装置(ハード) FREUND Academy 2023.03.17
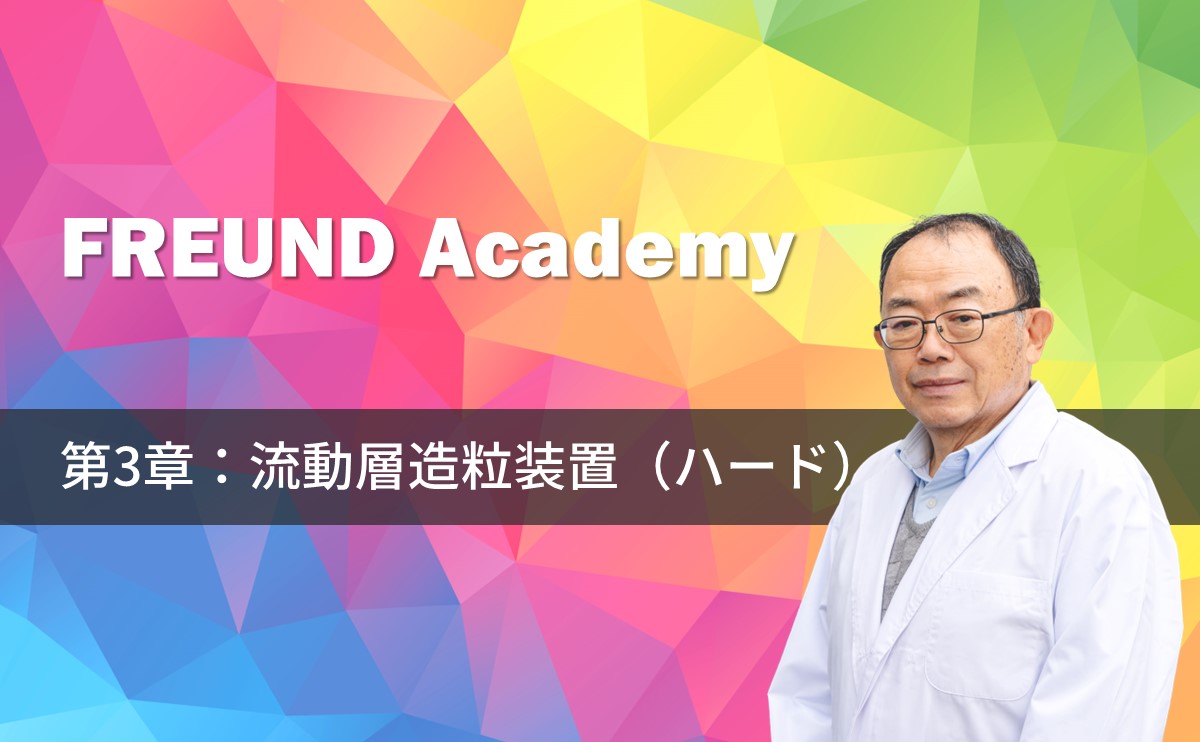
FREUND KNOWLEDGE OCEANをご覧頂き誠にありがとうございます。
FREUND Academy Instructorの武井でございます。
このFREUND Academyでは、製剤に関するベーシックな知識を全10章に分けてお送りいたします。
第2章で造粒について広く学ばれた皆さまに、今回の第3章では流動層造粒装置(ハード)、次回第4章は流動層造粒技術(ソフト)と、2回に分けて流動層造粒についてお伝えして参ります。
記事下部にて、流動層造粒装置の封じ込め技術(コンテインメント)の情報をまとめましたホワイトペーパーをダウンロードいただけますので、今回も最後までお付き合いください。
未読の方は、第1章:製剤とは? 、第2章:造粒と乾燥も是非ご覧ください。
流動層造粒装置の概略図を図1に示します。吸気口から導入された空気は、目皿板(スクリーンや分散板とも呼ばれます)を通って装置内に流入します。装置内部にはスプレーガンが設置され、バインダー液やコーティング液を噴霧します。微粉が装置外に飛散しないように本体上部にはバグフィルターが取り付けられています。また、万一、装置内で爆発が発生した場合に、爆発圧力による作業者への被害および装置破壊を防止するため、本体上部には爆圧放散口が設けられています。
1.1 目皿板
目皿板は、装置内の粉粒体が下部に落下することを防止するとともに、導入された空気が装置内の一部分から吹き抜けることなく、空気を装置内に均一に分散させる役目も担っています。通常、目皿板は金網と補強板の2枚で構成されています。金網の標準仕様は平畳織(ひらたたみおり、略して畳織)の42×175メッシュですが、他のメッシュサイズや平織りの金網も用いられます(図2)。補強板には目開きの大きい(線径の太い)平織りの金網やパンチング板が使われます。金網と補強板は、両者の間に入り込む粉体を洗浄できるように、通常は、溶接などで接着することなく重ね合わせて使用されます。
まれに、金網では微粉の目詰まりが懸念される場合に、断面が逆三角形のワイヤを横に並べたウェッジワイヤ(図3)が使われることもあります。
また、自動排出を促進するための風向板(コニダープレート)や遠心力による排出促進と吹き抜け防止作用のある旋回目皿(図4)が採用されることもあります。
1.2 スプレーノズル
液体をスプレーするノズルには、主に一流体ノズル(エアレスノズル、加圧ノズルとも呼ばれます)と二流体ノズルが使用されています。一流体ノズルは液圧の力で液体を霧化させるノズルで、過去に造粒コーティングに使用された実績はありますが、現在はほとんど使われておりません。その理由は、液体を霧化するには一定の液圧を確保する必要がありますが、ノズル径によって適正スプレー速度が異なるため、①スプレー速度の可変幅が小さい、②分散液によるノズル出口の摩耗が原因で、スプレーミスト径が変化するといった問題があるためです。
当社のスプレーノズルは二流体ノズルに属し、一例を図5に示します。二流体とは液体と気体を意味し、圧縮空気で液体を微粒化するノズルです。海外の生産機では、一本のアームの先端に複数(おもに3~6本)のノズルを付けた多頭ノズル(図6)が多く採用されますが、各ノズルから吐出される液量が均一であることが担保されない(したがってミスト径が担保されない)という理由で、国内での採用は多くありません。
1.3 バグフィルター
流動層造粒装置(フローコーター、スパイラフロー)の全ライン圧力損失(通気抵抗による圧力低下)は、吸排気ライン(空調機、ダクト、集塵機など)、目皿板、流動層、バグフィルターそれぞれの圧力損失の総和になります。
バグフィルター以外の圧力損失は、風量が変わらない条件下では、造粒乾燥中ほぼ一定です。そのため、造粒中の風量変動に伴うトラブルは、バグフィルターの目詰まりに起因することがメインです。目詰まりが起きると空気が流れにくくなり、それでも風量を確保しようとしてブロアの負荷が増加します。そうなると、圧力損失が大きくなりますが、風量はさほど増えないので正常な流動層が形成されなくなります。
そこで、バグフィルターのろ布が目詰まりしないように、ろ布表面に付着した粒子を定期的に払い落とす必要があり、払落し方法には「シェーキング」と「パルスジェット(圧縮空気による逆洗)」の2方式があります。
シェーキングとは、一定間隔(通常1~5分間隔)で流動を停止し、バグフィルターを昇降運動(所要時間15~30秒、5往復程度)させることで粒子を払い落とす方法です。
パルスジェットとは、通気中のフィルターに気流と反対方向から通気量よりも大量の圧縮空気を噴射し、フィルターを膨らませることで粒子を払い落とす方法で、圧縮空気を逆方向に噴射することから逆洗(逆流洗浄)と呼ばれています。
逆洗は通常0.5~1分間隔で、圧縮空気の噴射時間は0.5秒程度です。逆洗するフィルターは2~10系統に分けられ、1系統ずつ順番に逆洗します。逆洗する対象以外の系統のフィルターは通気状態なので、払落しのために流動を停止する必要がありません。
シェーキング式バグフィルターの外観を図7に、シェーキング動作のイメージを図8に示します。
バグフィルター室を2分割し、それぞれの部屋のバグフィルターを交互にシェーキングすることにより、流動を止める必要がない2室分離型バグフィルターの概略を図9に示します。
パルスジェット式バグフィルターには円筒型、ポケット(封筒、座布団)型、カートリッジ型があります。
ポケット型とカートリッジ型バグフィルターの外観を図10に、パルスジェット動作のイメージを図11に示します。
収率・耐久性を向上させた新しいバグフィルターを取り扱っております。
↓↓↓ 是非、下記リンクより詳細記事をご覧くださいませ。 ↓↓↓
2.1 流動層の定義
金網などの目皿板上に粉や粒子(以下、粒子という)をのせ、下方より空気を流入させると粒子は浮かび上がり、空気との混合層が形成されます。このときの粒子と空気は、あたかも液体が沸騰しているように流動しています。このような状態の固気混合層を流動層(Fluidized bed)といいます。
流動層造粒装置(たとえばフローコーター)に粉粒体を充填し、空気を流入させると、風速の増加にしたがって固定層(充填層)→ 流動層 → 移動層(輸送層)と変化していきます。
① 固定層(Fixed bed)
目皿板に送られた空気は整流され、小さな気泡となって粒子の間隙を通り抜けます。風速が小さいうちは粒子は浮かび上がらず、固定した状態で留まっています。この状態を固定層と呼びます。風速を上げると通気抵抗が高まっていきます。
② 流動化開始速度Umf (minimum Fluidized velocity)
固定層を流れる風速が大きくなっていくと、ついにある時点で充填した粉粒体の表面が「ブクブク」と動き始めます。空気も小さい泡となって粒子表面を通過していきます。このときが流動化の始まりで、このときの風速を「流動化開始速度Umf」と呼びます。
③ 流動層(Fluidized bed)
流動化開始速度より流速が大きくなると、ついに粒子は浮かび上がり上下運動をするようになります。この状態が流動層です。さらに風速を大きくすると、粒子の浮遊も高くなります。フローコーターやスパイラフローで造粒する場合、流動状態の高さは固定層高さの2倍程度が適当です。
2.2 流動層の圧力損失(⊿P)
目皿板の真下と流動層の上部を管でつなぎ、U字型のガラス管(U字管マノメータ)内に水を封入して、流動層内に空気を流した場合を考えてみます(図13)。まず空気が目皿板を通過するときに抵抗を受けるので空気の圧力が降下します。つぎに粒子層を流動化させるために粒子層の重量(仕込量)に応じて圧力が降下します。さらに空気がバグフィルターを通過するときも圧力は下がります。こうした圧力降下を「圧力損失」(差圧)と呼び、⊿P(デルタ ピー)で表わします。圧力損失はU字管の水の高さとなって測定できます(通常は差圧計=マノメータを使います)。粒子を投入せずに測定し、粒子を投入した場合と比較すれば、流動層を形成するための圧力損失がわかります。また、バグフィルターの前後の位置にマノメータをつなげれば、バグフィルターの圧力損失が測定できます。こうした各部の圧力損失の測定は、仕込量やブロアを選定するうえで重要です。
ダクトや目皿板、バグフィルター部分は、風速が大きくなると圧力損失も大きくなるので、ブロアの選定には風量だけでなく、それに見合った静圧を考慮しなければなりません。(大きな風量のブロアを選定しても、ブロアの静圧が小さいと、通気抵抗に負け所定の風量は流れません)。
一方、固定層→流動層→移動層への移行を圧力損失の変化でみると図14のようになります。(図の縦軸⊿Pは粒子層による圧力損失を表し、目皿板やバグフィルターの圧力損失は含まれていません)。
① 粒子投入前の目皿板の圧力損失については、ふつう流動層の⊿Pの10%以上が必要とされています。目皿板の⊿Pが小さすぎると空気が目皿板全体に広がらず、一部分から流れてチャンネリング現象(吹き抜け現象)を引き起こし、粒子全体が浮かび上がらず正常な流動層を形成できません。
② 粒子を投入し風速をしだいに大きくしていくと、粒子は固定層のままで浮かび上がりませんが、粒子層の⊿Pは大きくなっていきます(A→B)。
③ C点は先に述べた流動化開始速度(Umf)で、粒子の流動化が始まります。流動層が形成されると、いったん⊿Pは下がりますが以後は風速を大きくしても、粒子層の⊿Pはほぼ一定を保ちます(C→D)(あくまで粒子層を流動化する⊿Pの話で、目皿板やバグフィルターの⊿Pは風速とともに増加します)。フローコーターで正常な運動をする場合の風速は、流動化開始速度(Umf)の2~4倍程度です。一般的な医薬品、食品原料で流動層を形成する場合、目皿板部分の空塔速度(線速)は1.0m/s、フィルターケーシング部分の空塔速度は0.5m/sが目安になります。
※空塔速度とは、風量を通気断面積で割った速度。流動層装置内には目皿板やスプレーガンなどの気流が通過できない部品が装着されているが、こうした妨害物がない場合(空塔)を想定した速度を示す。
④ 風速をさらに大きくすると、粒子の動きは激しくなり⊿Pも少し大きくなります(D→E)。この状態はフローコーターでは正常な運転ではありません。Fは終末速度(Ut)で粒子は徐々に移動層(輸送層)に移行し、やがてすべての粒子が飛ばされてしまい、粒子層の⊿Pは消失(=粒子層が消失)します。
2.3 流動層の仕込量と圧力損失(⊿P)の関係
図13の測定モデルにおいて、空運転時の目皿板とバグフィルターの⊿Pを求めれば、残りの⊿Pは流動層を形成するためのものと考えられます。流動層が形成されている間は、風速、粒子形状、粒子径、粒度分布に関係なく、流動層を形成する(粒子を浮遊させる)圧力損失はほぼ一定値を示し、おおよその値は次式で計算できます。(仕込重量を空気が支えているという考え方です)。
↓↓↓ 更に詳しく学びたい方へ資料をご準備しております。下記よりダウンロード可能です ↓↓↓
第3章からは、より具体的な内容となり、流動層造粒装置の構造と流動層の形成についてお送りしました。
最後までお読みいただきありがとうございました。
次回、第4章は流動層造粒技術(ソフト)についてお伝えします。
このコンテンツが製薬業界の更なる進歩発展の一助となれますよう、心を込めて執筆いたします。
次回もお付き合いくださいますよう、よろしくお願い申し上げます。
↓↓↓ この記事に関するご意見・ご質問は、下記よりお気軽にお問合せくださいませ。 ↓↓↓
キーワード: