覚えておきたい製剤技術の基礎知識! 第4章:流動層造粒技術(ソフト) FREUND Academy 2023.06.27
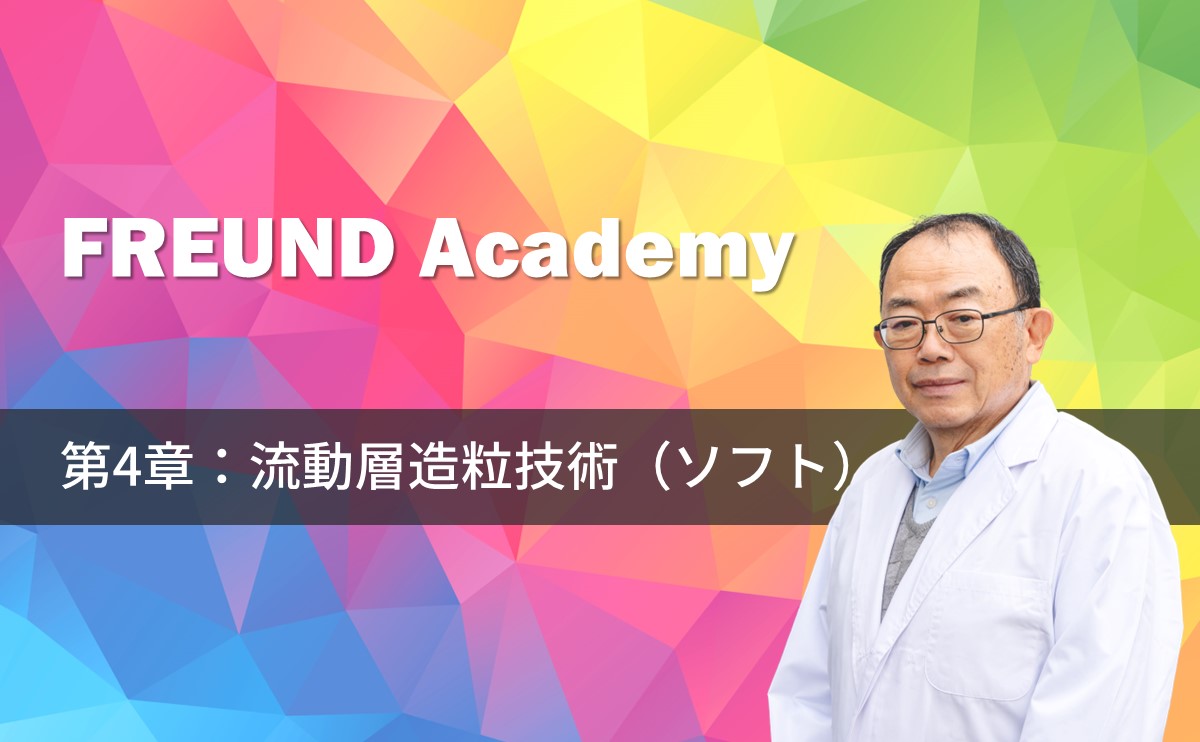
FREUND KNOWLEDGE OCEANをご覧頂き誠にありがとうございます。
FREUND Academy Instructorの武井でございます。
このFREUND Academyでは、製剤に関するベーシックな知識を全10章に分けてお送りいたします。
前回、第3章では流動層造粒装置についてお伝えしました。続く第4章は流動層造粒技術(ソフト)と題して、流動層造粒について詳しくお伝えして参ります。
記事下部にて、流動層造粒高速化の情報をまとめましたホワイトペーパーをダウンロードいただけますので、最後までお付き合いください。
未読の方は、第1章:製剤とは? 、第2章:造粒と乾燥、第3章:流動層造粒装置(ハード)も是非ご覧ください。
-
1.凝集造粒のキーワード
1.1 造粒水分
1.2 水分蓄積速度
1.3 結合剤
1.4 スプレーミスト径
1.5 局所濡れ
2.スケールアップ
2.1 フローコーターのスケールアップ
2.2 スケールアップの留意点
流動層造粒とは、流動化している粉粒体にバインダー(結合剤)液を噴霧して、粉粒体の凝集造粒を行う操作です。造粒製品に求められる物性には、平均粒子径、粒度分布、かさ密度、流動性、溶解性などがあり、所望の物性を得る方法について、次の5つのキーワード「造粒水分」「水分蓄積速度」「結合剤」「スプレーミスト径」「局所濡れ」に分けて説明します1) 。
1.1 造粒水分
一般に、造粒水分とは造粒中の粉粒体に含まれる水分を意味します。造粒水分と乾燥後に得られる製品の平均粒子径の間には相関関係が認められます。
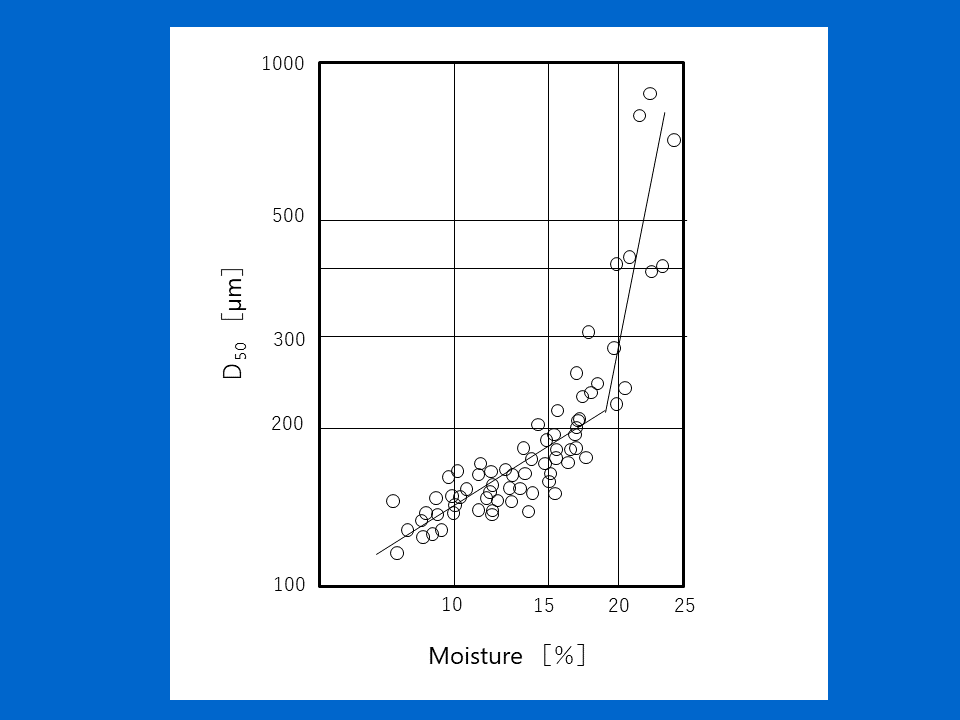
図1は、乳糖:コーンスターチ(8:2)の混合末を、ヒドロキシプロピルセルロース(HPC-L)水溶液で造粒した時の、造粒水分と平均粒子径の関係を示しています。
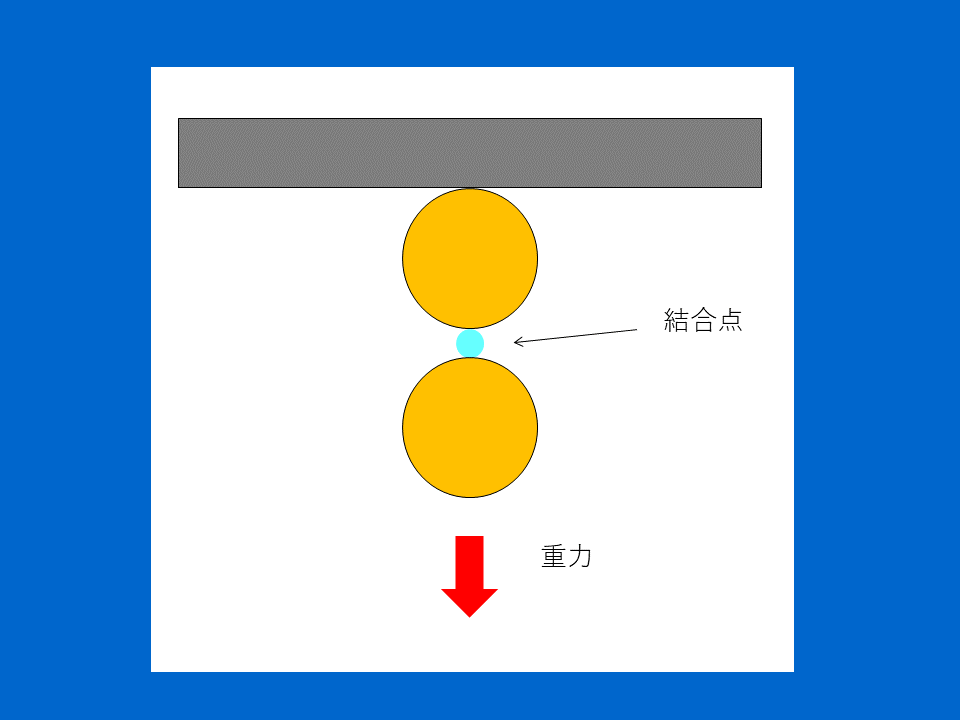
凝集造粒物の粒子径を決定する要因は、粒子間にはたらく付着力と分離力のバランスと考えられます。粒子間にはたらく付着力は、液体架橋を形成するための水分量に依存し、粒子間にはたらく分離力とは凝集粒子の重量と言われています。上板に接着した粒子と、その下に付着した粒子間の結合点にはたらく分離力は、下側の粒子の重量と考えられます(図2)。
これらのことから、次の通り定義付けられます。
- 粒子を凝集しようとする力(付着力):粒子間に形成される液体架橋の強度で、粒子の表面積に比例(粒子径の2乗に比例)
- 粒子を引き離そうとする力(分離力):粒子の重量で、粒子の体積に比例(粒子径の3乗に比例)
付着力は粒子径の2乗に比例し、分離力は粒子径の3乗に比例するので、粒子どうしが付着するか分離するかの境界は、粒子径によって決まります。
図3に示すように、粒子径が小さいときは付着力>分離力となり造粒が進行しますが、粒子が成長すると付着力<分離力となるので、粒子が接触してもすぐに分離し、造粒の進行は停止します。
付着力は造粒水分に関係するので、付着力>分離力と付着力<分離力の境は、水分量によって変化します。こうした造粒水分と平均粒子径の関係を把握したうえで、水分計測による造粒のプロセス制御(PAT)も行われています。
※PAT(Process Analytical Technology)
リアルタイムな計測により、医薬品の製造工程の設計、分析、管理を行い、最終的に製品の品質を保証するシステム
一方、造粒水分は、造粒物のかさ密度にも影響を及ぼします。一般に、造粒水分値が高いと造粒物のかさ密度は大きくなります。また、同じ造粒水分値であっても、粒子群にかかる圧密作用により、造粒物のかさ密度は変化します2)。
図4の右列に示すように、造粒中の粒子の動きが激しいと圧密作用が働き、湿潤粒子内の粒子間距離が小さくなり、重質な造粒物が得られます。
これに対し、図4の中央列に示すように粒子の動きが緩慢な場合は、湿潤粒子内の粒子間距離が大きいままで(したがって湿潤粒子内の空隙率も大きく)、軽質な造粒物になります。
さらに、結合剤の付着力が弱い場合、図4の左列に示すように、湿潤状態では結合剤の付着力と水分の付着力により2次粒子を形成しますが、乾燥工程で水分が除去されると、結合剤の付着力だけでは2次粒子を維持できず粉化してしまいます。このように、乾燥工程で粉化する湿潤粒子は、見かけの凝集と呼ばれます。
1.3 結合剤
流動層造粒における結合剤(バインダー)液の役割は大きく、水のみで造粒する場合もありますが、所望の粒子径や粒子強度を得るためには結合剤が必要になります。
前項で説明した見かけの凝集を克服し付着力を大きくするためには、造粒水分の調整だけでは限界がありますが、結合剤の濃度を高くすることにより簡単に解決することもあります。たとえば、5%ヒドロキシプロピルセルロース(HPC-L)水溶液では難しい造粒が、10%HPC-L水溶液では簡単に造粒できるケースもあります。
一般に、結合剤粘度が高いほど造粒はしやすいのですが、得られる造粒物は軽質になる傾向があります。スパイラフローのように圧密作用のある造粒装置ではその傾向が顕著です。
1.4 スプレーミスト径
造粒物性に影響を及ぼす要因として、結合液のスプレーミスト径が知られています。
一般に、適正範囲内であれば、ミスト径と粒子径の間には正の相関があります。流動層造粒装置で多用される二流体ノズルでは、得られるミスト径は霧化用のスプレー空気量(圧縮空気供給速度)とスプレー液速度(スプレー液供給速度)との噴出速度差で決まります。
二流体ノズルを使って、8%ヒドロキシプロピルメチルセルロース(TC-5R)水溶液をスプレーし、レーザー散乱式粒子径測定装置で液滴径を測定したときの気液比と平均ミスト径の関係を図5に示します。また、主な測定条件を表1に示します。
スプレー液速度を固定した場合(図5の①~④)、気液比と平均ミスト径の間には、良好な相関関係が成立しますが、スプレー空気量を固定した場合には(図5のA~C)、気液比を変化させても(具体的には、スプレー液速度を変化させても)、平均ミスト径はほとんど変化しないことがわかります。
二流体ノズルでは、液体を微粒化するためのエネルギー供給源は、圧縮空気の運動エネルギーと考えられます。たとえば、液速度を4倍にする場合、同じミスト径を得るためには圧縮空気の運動エネルギーも4倍にする必要がありますが、運動エネルギー(1/2mv2)は速度の2乗に比例するので、圧縮空気の速度は2倍にすればよいことになります。
したがって、スプレー空気量を変化させるほうが、スプレー液速度を変化させるよりも、得られるミスト径の変化量が大きくなります。
1.5 局所濡れ
流動層造粒では、造粒水分の管理が重要であることを説明しましたが、装置内の平均的な造粒水分だけでなく、局所的な現象(局所濡れ、Local Wetting)にも留意する必要があります。
流動層造粒装置では、装置が大きくなるほど単位仕込量当たりの供給風量は小さくなり、スプレーノズル1本当たりの給液速度は大きくなります。すなわち、装置の大型化に伴い、単位仕込量当たりの撹拌混合能力は小さくなり、スプレー給液速度は大きくなるので、とくに大型機では局所濡れが発生しやすいことが示唆されます。
たとえば、造粒水分と平均粒子径の関係を示した本章の図1は、低水分域(造粒適正水分域の下限以下と考えられる領域)から徐々に造粒が進行しています。この現象は局所濡れに起因していると考えられます。つまり、粒子層内の水分は粒子層全体では造粒適正水分に到達していなくても、スプレーが粒子に直接接触する領域(スプレーゾーン)では、局所的に造粒適正水分に到達していることが推察されます。
図6は流動層造粒装置を使用し、乳糖:コーンスターチ(7:3)の混合末をHPC-L水溶液で造粒した時の、造粒水分と平均粒子径の関係です3)。
スプレー液速度が250g/min以下の場合とそれ以上の場合では、造粒水分と平均粒子径の関係が一致しません。この現象はスプレーミスト径の影響もさることながら、局所濡れの影響も大きいと考えられます。
スケールアップの条件設定の要因には風量、スプレー液速度、仕込量、乾燥時間、スプレー空気(霧化空気=アトマイズエアー)量等があります。
通常は給気(吸気)温度、排気温度、バインダー等は固定条件となります。造粒コーティング操作では「濡れと乾燥」、それに伴う造粒水分の管理が主要因としてあり、スケールアップ計算の根底となります。以下、フローコーターのスケールアップ計算を説明します。
2.1 フローコーターのスケールアップ
以下、簡易法でFLO(F)-5型からFLO(F)-120型へのスケールアップ計算例を紹介します。
(1)仕込量
原料容器(コンテナ)容量の60%前後が、一般的な仕込量です。
フローコーターの型式につけられている数字は、かさ密度0.5g/mLの粉体の仕込重量を表わしています。FLO(F)-5型は5kg、FLO(F)-120型は120kgが適正仕込量の目安になります。
仕込量のスケールアップの基本は、装置直径の3乗に比例させます(図7A)。いわゆる相似形でのスケールアップは、流動層形成(流動不良の防止)の重要な要因になります。仕込高さを一定にしたスケールアップ(図7B)は、吹き抜けによる流動不良の原因になります。
標準操作では相似形仕込量でスケールアップしますが、その場合仕込高さが大きくなるので、粒子の自重による圧密効果が大きくなり、生産機ではテスト機よりも造粒物のかさ密度が大きくなる傾向があり、この傾向は、とくにシェーキング式装置で顕著です。
(2)バインダー量
実験に用いた使用量を仕込量の重量に比例させてアップします。
FLO(F)-5型で5kg仕込の時とき1Lのバインダーを使用したとすれば、FLO(F)-120型で120kg仕込では【120÷5×1=24】で24Lとなります。
(3)風量
スプレーケーシング部の空塔速度を同一に設定します。
FLO(F)-120型の装置直径(スプレーケーシング直径)はFLO(F)-5型の装置直径の3倍なので、風量は装置断面積に比例させて9倍にするのが標準です。
(4)給気温度、湿度
製品品質に影響がないよう、また、濡れと乾燥のバランスを基礎データと同じにするためにも給気温度、湿度は基礎データと同じにすることが望まれます。
通常、流動層造粒では製品温度(≒排気温度)は給気の露点になるので、直接の制御因子には含まれません。
(5)スプレー速度
濡れと乾燥のバランスを基礎データと同じにするためには、スプレー液速度は給気風量(=乾燥能力)に比例させます。
バインダー量が仕込量に比例(すなわち装置直径の3乗に比例)しているのに対し、スプレー液速度が風量に比例(すなわち装置直径の2乗に比例)しているので、装置直径に比例してスプレー時間が延びます。(乾燥時間も同様に延びます)。
(6)造粒・乾燥時間
上述したように、装置直径に比例して造粒・乾燥時間は長くなります。
乾燥時間について厳密には、減率乾燥期間では粒子内の水分移動が律速になることもあり、計算結果と実際の乾燥時間はわずかにずれることもあります。また、小型機と大型機では仕込量に対する装置の比表面積が異なる(大型機のほうが小さい)ので、装置壁面からの放熱量が異なり(単位仕込み量当たりの放熱量は大型機のほうが小さく)、計算値より大型機の乾燥時間は短くなる傾向があります。
(7)スプレー空気圧と空気量
バインダーをスプレーしたときの液滴径は通常10~50μmです。
液滴が粗くなると造粒物は粗大粒子になりやすく、粒度分布はブロードになる傾向があります。スプレー空気の圧力は、大型機では0.4MPa前後、小型機では0.3MPa前後が適当です。所望の液滴径を得るポイントはスプレー空気量(供給速度)であり、バインダー液の供給速度との関係を、レーザー散乱式粒子径測定装置などを用いて測定することが望まれます。
2.2 スケールアップ時の留意点
局所濡れの解消は、スケールアップ時の重要な因子でもあります4)。小型機で適正な造粒水分と適正なスプレー液速度の条件が取得できた場合のスケールアップの留意点について、図8を使って説明します。
小型機(たとえばFLO(F)-5型)では仕込み容積に対するスプレーゾーンの領域が大きく、水分の粒子層内への拡散が速いため、局所濡れの影響はあまりありません。大型機の装置内では粒子層全体への水分の拡散が小型機に比べ遅くなるので、粒子層内の水分の平均値とスプレーゾーン内の水分値の乖離幅は小型機に比べ大きくなります。
したがって、スプレーゾーン内の水分値を小型機と同等にスケールアップするためには、大型機では粒子層内の平均水分値を小型機に比べやや小さくする場合があります(スケールアップ1)。極論すれば、小型機では粒子層全体で造粒が進行するのに比べ、大型機ではスプレーゾーン内でのみ造粒が進行すると言えます。この方法は水分に敏感な原料でとくに有効です。
粒子層内の平均水分値を小型機と同じ値にしてスケールアップした場合、スプレー液速度が適正であっても(スケールアップ2)、スプレーゾーン内の造粒水分はやや過多になり、粗大粒が発生するリスクが大きくなります。さらに、1ノズル当たりのスプレー液速度を大きくすると(スケールアップ3)、粒子層の水分が過多になり、ブロッキングが発生し、流動停止につながるケースも考えられます。
↓↓↓ 更に詳しく学びたい方へ資料をご準備しております。下記よりダウンロード可能です ↓↓↓
第4章は、流動層造粒について求められる物性や、所望の物性を得る方法について、重要となるキーワードに分けてご説明しました。
最後までお読みいただきありがとうございました。
次回、第5章は錠剤コーティング装置(ハード)についてお伝えします。
このコンテンツが製薬業界の更なる進歩発展の一助となれますよう、心を込めて執筆いたします。
次回もお付き合いくださいますよう、よろしくお願い申し上げます。
参考文献
1)武井成通:PHARM TECH JAPAN,18,927(2002)
2)粉体機器・装置ハンドブック:P411,日刊工業新聞社(1995)
3)沢口直司、小林 賢:PHARM TECH JAPAN,7,927(1991)
4)栗田雄二、鵜野澤一臣、武井成通:PHARM TECH JAPAN,20,1377(2004)
↓↓↓ この記事に関するご意見・ご質問は、下記よりお気軽にお問合せくださいませ。 ↓↓↓
キーワード: