連続生産システム
原料投入から造粒、整粒、乾燥、滑沢剤混合、打錠までをスピーディかつ連続的に一貫生産できるシステムです。
バッチ生産から連続生産にシフトすることで、生産性向上、品質安定化、コスト・時間・スペースの削減を実現します。
造粒工程は、湿式と乾式の両方に対応しています。
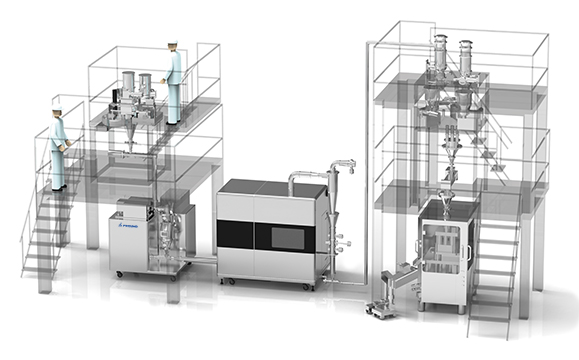
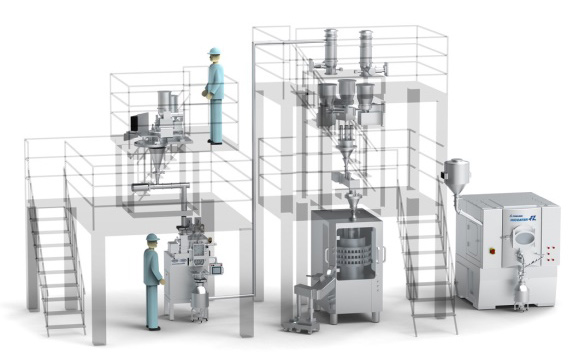
特長
1.State of Control Systemによる品質管理
製造工程中の品質をPATツールで常時モニタリングし、品質管理範囲からの逸脱前に運転条件を自動調整(フィードバック制御)します。
品質の安定した製品を、必要な時に必要なだけ生産できます。
2.スケールアップ不要 (スケールアウト)
異なるスケール、および同一スケールの装置間で、製品の同等性が確保でき、開発段階から商用生産へのスケールアップの検討を省略することが可能になります。
3.PATツールによる少量での測定
バッチ生産では各工程の管理試験が必要ですが、連続湿式・乾式造粒機ではPAT検出部にて少量(1L単位)で測定を実施します。バッチ生産のように大量生産する前に、品質基準を満たさないものを排出し、製造ロスを削減します。
近赤外分光計(NIRs)と粒度分布測定装置により、品質のモニタリングが可能です。
4.フットプリントを削減
必要な装置類を連続生産システムへ移行することで、設置面積を大幅に削減、スペースを有効利用できます。
例)1/3以下に削減
従来型流動層ライン(総面積170 ㎡)
(流動層造粒乾燥機、整粒機、V型混合機、顆粒用コンテナ、打錠機)
↓
連続生産システム(造粒部~乾燥部~打錠機)(総面積50 ㎡)
5.中間倉庫を不要に
バッチ生産では、中間製を容器などへ回収し、中間倉庫へ保管、工程検査の後、次の工程へ運びますが、連続生産システムではこの作業が省略できます。