混合・造粒・乾燥
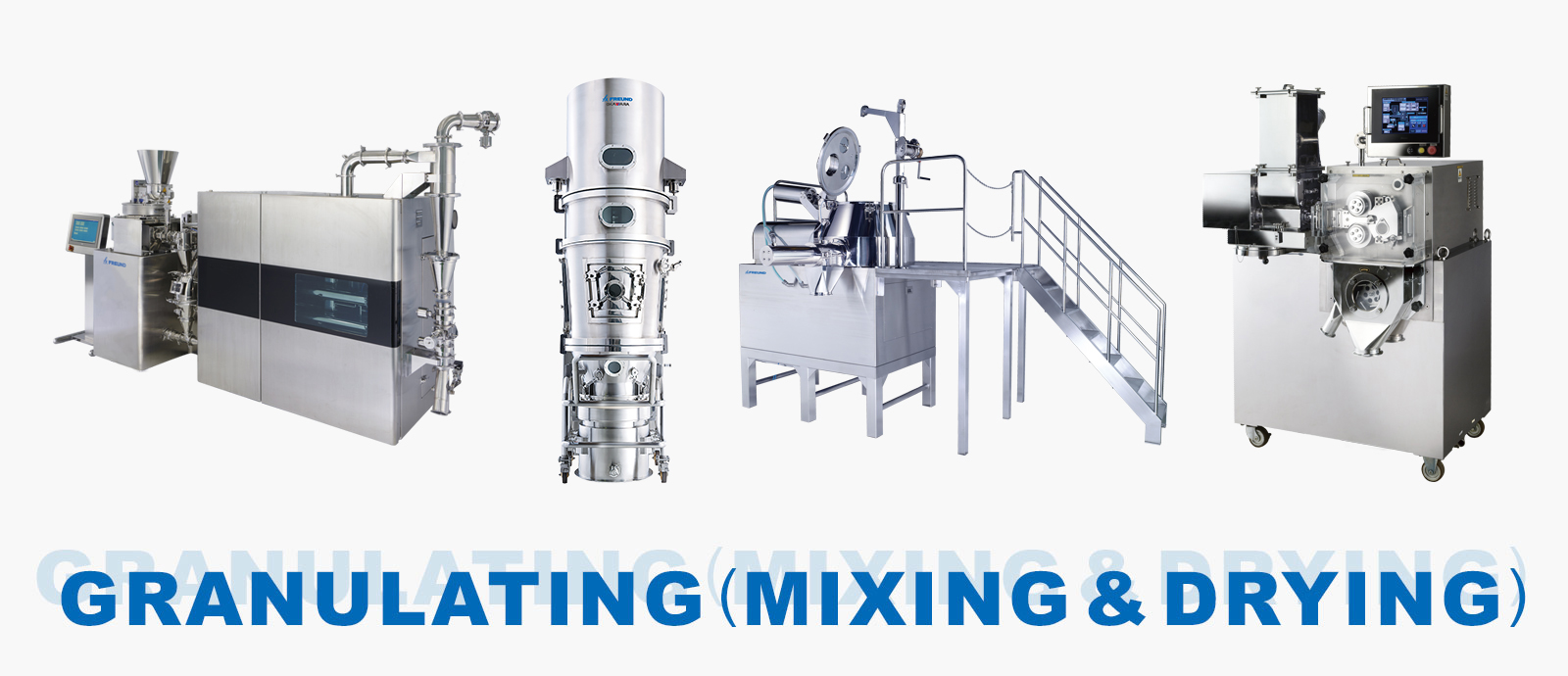
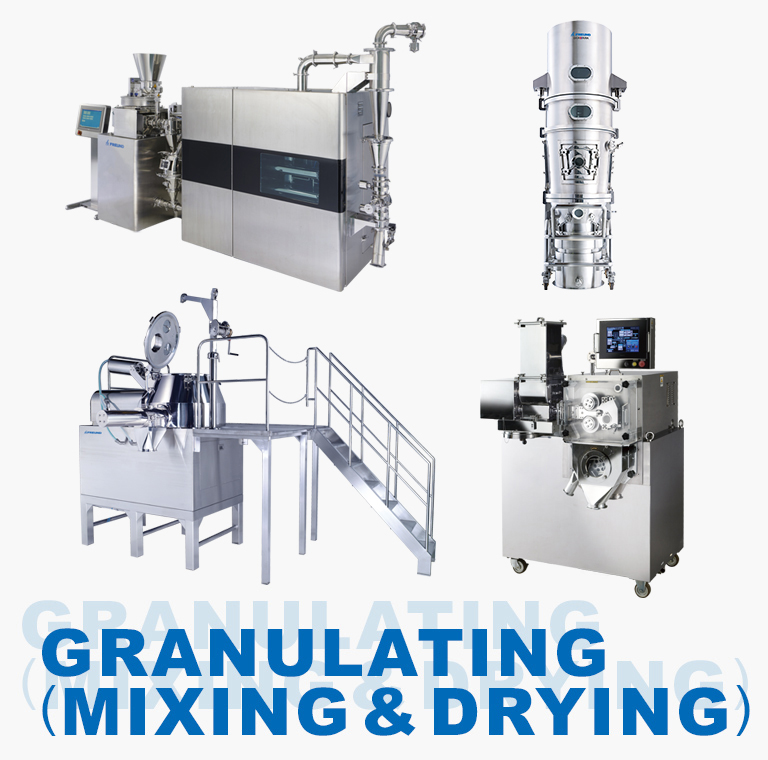
混合
混合とは、2種類以上の粉粒体を、乾燥状態あるいは少量の液体を加えた状態で混ぜ合わせ、含まれる成分を均一な状態にすることです。混合の良不良は最終製品に影響を及ぼします。
なお混合の目的(造粒前の予備的な混合か、打錠やカプセル充填前の最終混合か)により、必要とされる均一度や評価法は変わります。
造粒
造粒とは、原料から目的とする大きさの“粒”をつくる工程です。
主に次の問題解決を目的として行われます。
医薬品原料は、一般に流動性が悪く、粉同士がくっつきやすく、取り扱いにくいという性質があります。このような取り扱いにくい性質を改善するために造粒します。また造粒により、圧縮特性(打錠性)を改善したり、時には溶解性を改善したりすることができる場合もあります。さらに、原薬の偏析を防止して、製剤均一性(含量均一性)を改善するために造粒する場合もあります。
造粒には主に2つの方法があり、造粒方法や使用する装置を原料や目的にあわせて選びます。
湿式造粒
- 原料微粉末へ接着するための液体を加えて粒子同士を結合させ、その後水分を乾燥させて大きな粒をつくります。現在、日本で広く採用されている湿式造粒法には主に次の2つがあります。
原料を結合剤溶液で混錬し、これをスクリーンから押し出して造粒します。連続式の場合は必ずしもスクリーンを通すことなく、混錬機からスクリューによってそのまま排出する方法が多く採られています。排出された湿塊粒は、必要に応じて湿式解砕し、続いて乾燥機により乾燥します。
装置としては、一般的な流動層造粒装置の製品容器の下部にローターを設け、これを回転させることにより、顆粒に圧密効果を与え、嵩密度を高くするものです。
乾式造粒
- 原料をロールで圧縮してフレーク状にした後、粉砕することで目的の大きさの粒をつくります。水分や溶媒に弱い原料、風味を保ちたい原料を造粒するのに向いています。
コーティング方法としては、側方噴霧法、ワースターコーティング法、転動流動コーティング法などがあります。
製品一覧 LINEUP
-
-
-
Granuformer (グラニュフォーマー)
造粒・整粒・乾燥工程を集約した湿式連続生産装置です。バッチ生産から連続生産へのシフトで、コスト・時間・スペースの削減や品質の安定化を実現します。
-
-
-
-
FLO-COATER(フローコーター)
流動層乾燥装置にスプレーシステムをドッキングした流動層造粒・乾燥・微粒子コーティング装置です。発売以来数多くの実績を誇り、絶大なる信頼を頂いております。
-
-
-
-
FLO-COATER (フローコーター高速造粒モデル)
流動層乾燥装置にスプレーシステムをドッキングした流動層造粒・乾燥・微粒子コーティング装置です。従来機に比べ、製造工程時間・ランニングコストを削減します。
-
-
-
-
FLO-COATER (フローコーター12bar)
国内初の生産用途で設置認可を取得した、爆発放散孔を必要としない12bar耐圧仕様の流動層造粒コーティング装置です。
-
-
-
-
Granurex (グラニュレックス)
1台で粉末被覆造粒・コーティング・乾燥のプロセスが可能な、遠心転動造粒コーティング装置です。
-
-
-
-
SPIR-A-FLOW(スパイラフロー)
遠心転動・浮遊流動・旋回流動・整粒の各種機能の複合化により、粒子形状、粒度分布およびかさ密度を自由にコントロール可能な複合型流動層造粒コーティング装置です。
-
-
-
-
GRANUMEIST (グラニュマイスト)
短時間造粒を可能にする高速攪拌造粒装置です。
-
-
-
-
BALANCE GRAN (バランスグラン)
混合・分散・混練・造粒・乾燥(※オプション)を同一容器内で処理できる、画期的な高速撹拌造粒装置です。
-
-
-
-
ROLLER COMPACTOR FP (ローラーコンパクターFP)
多様な原料に対応する乾式造粒装置です。分解組立・洗浄性に優れ、コンテインメントにも対応します。
-
-
-
-
ROLLER COMPACTOR TF (ローラーコンパクターTF)
多様な原料に対応する乾式造粒装置です。部品点数が少なく、非常に扱いやすい装置です。
-
-
-
-
ROLLER COMPACTOR FT (ローラーコンパクターFT)
多用な原料に対応する乾式造粒装置です。堅牢な構造で、造粒しにくい原料や、大容量の生産にも対応します。
-
-
-
-
SPHEREX(スフェレックス)
真球度が高く、継ぎ目のない粒径φ1~5 mmのシームレスミニカプセルを、高精度で製造する装置です。
-
-
-
-
製丸機
かぎりなく球に近い造粒を行い、幅広いサイズの丸薬およびカプセル状の粒を作製する装置です。
-
-
-
-
低湿棚型乾燥庫 LOW HUMI BOX DRIER
「温風・冷却除湿・デシカント除湿」のハイブリッド乾燥方式で加熱による劣化を防ぎ、対象物に対してダメージレス乾燥を行え、また棚の入れ替えが不要な棚式乾燥機です。
-